Using natural materials
General description
Natural materials are subdivided into bio- and geo-based materials. Central advantages of using bio-based materials in construction (e.g., timber, bamboo, straw, hemp) are their long-term storage of biogenic carbon and their renewable character. In combination with simple and reversible construction systems, they have a high recycling and reuse potential after the first end-of-life of a building. Also, geo-based materials (e.g., stones, soils) are beneficial, if produced in a way that makes reusing or recycling possible. For example dimensioned natural stones have a very long lifecycle with a high level of integrity while earth bricks are biodegradable.
Examples
TECLA
Massa Lombarda, Italy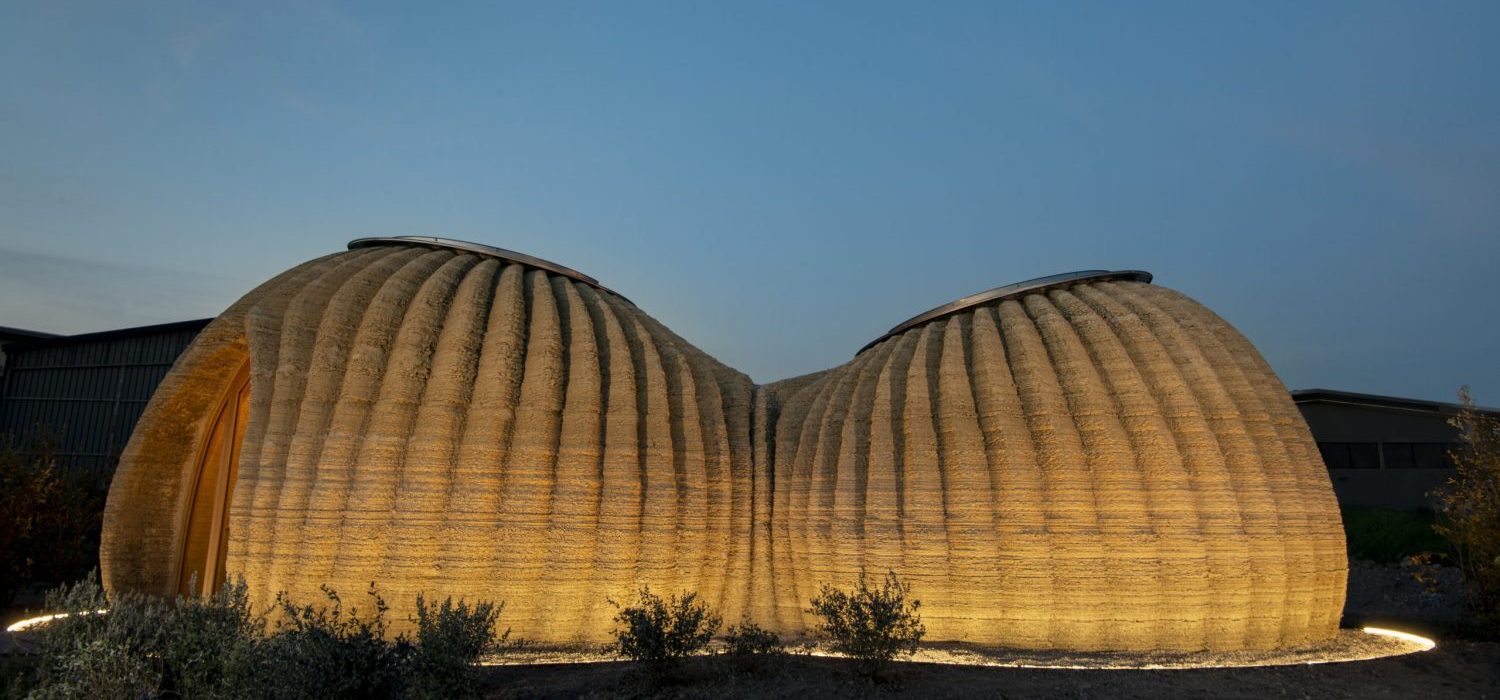
62% of the material used in the project is derived from renewable bio-based sources. Rice husk, the outer shell of rice, is utilised as insulation material for both the building's envelope and floor. Typically, rice husks are discarded as waste, but in this project, they have been repurposed into a building material, thereby reducing the CO2 footprint associated with rice husks. Normally, rice husks are either burned in fields or left to decompose, contributing to environmental emissions.
THE EDGE SÜDKREUZ
Berlin, Germany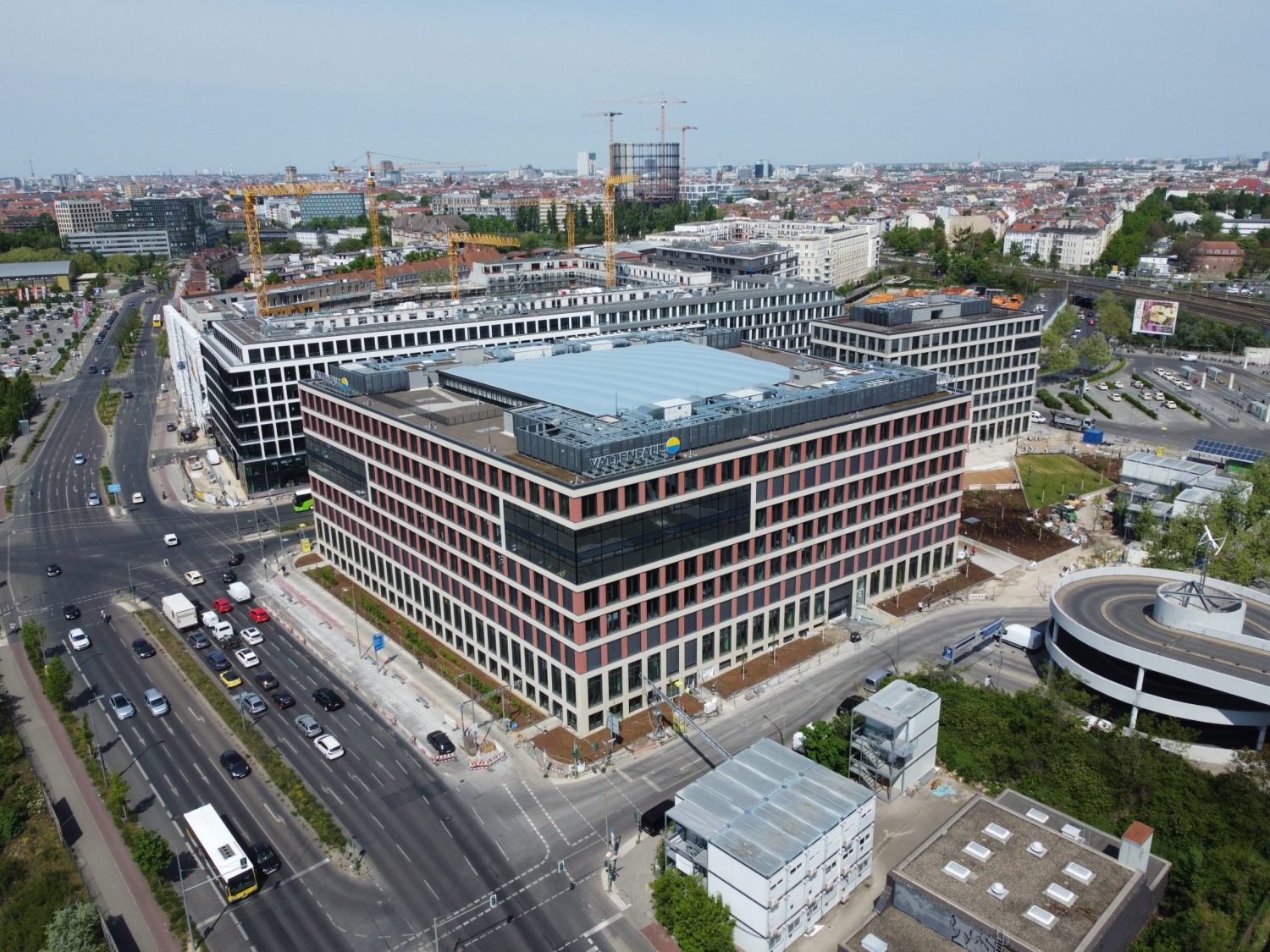
The structure of the building primarily consists of wood, with the exception of the cores, which remained in concrete due to regulations. All the forces, both horizontal and vertical, are carried by large wooden beams. A key aspect of constructing a sustainable building with wood is ensuring that the timber is sourced from certified plantations.
Résilience
Stains, France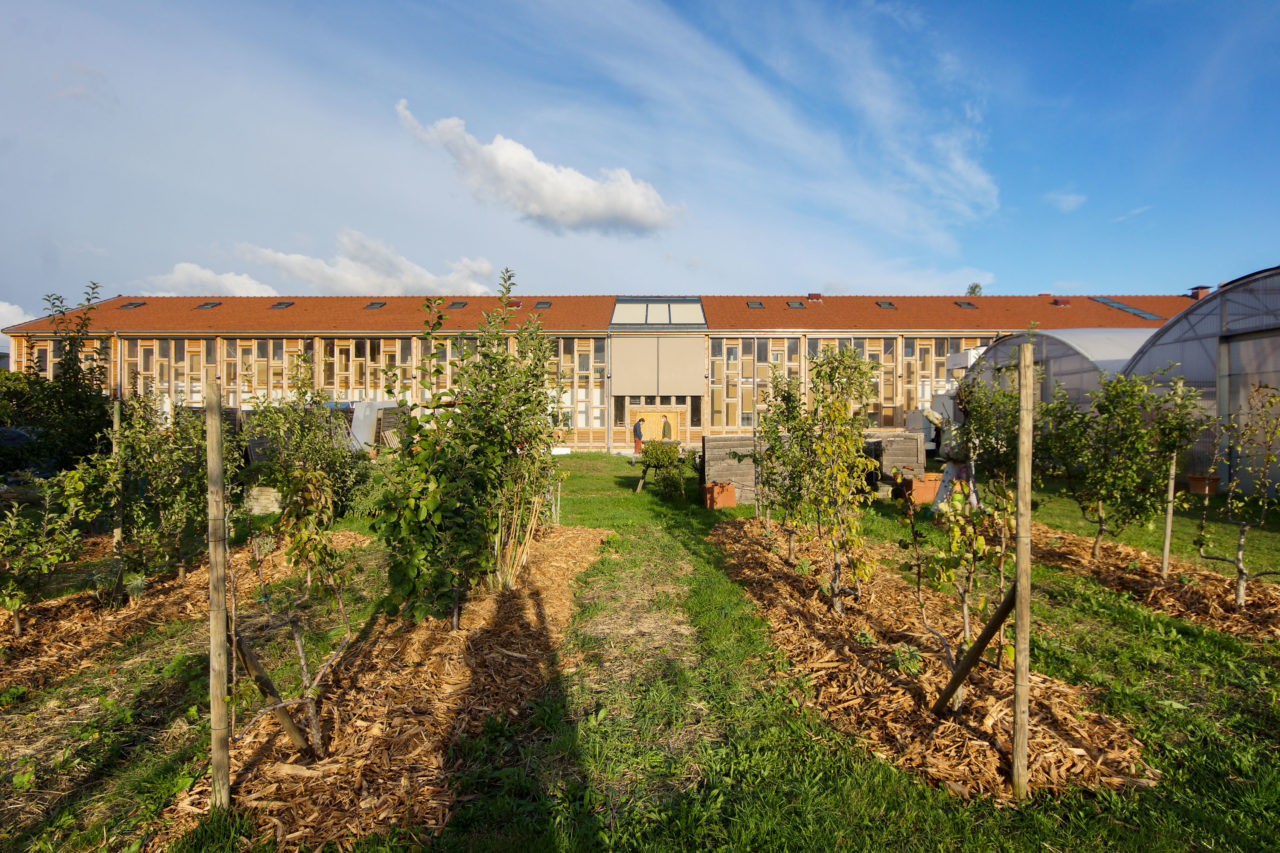
The structure of the building is constructed using wood sourced from French forests. The facade features prefabricated composite walls known as Ekoblocks, which consist of wooden caissons filled with compressed straw and coated with raw earth on both sides. The roof is insulated with wood wool. In a sustainable approach, the excavated earth from the construction site is reused in the project. It is mixed with recycled cellulose from cardboard boxes found on the site and applied as plaster on the walls. Additionally, this earth is combined with crushed reused concrete as an alternative to sand for stabilising the clay and constructing the rammed earth wall of the cafeteria.
Mjøstårnet
Brumunddal, Norway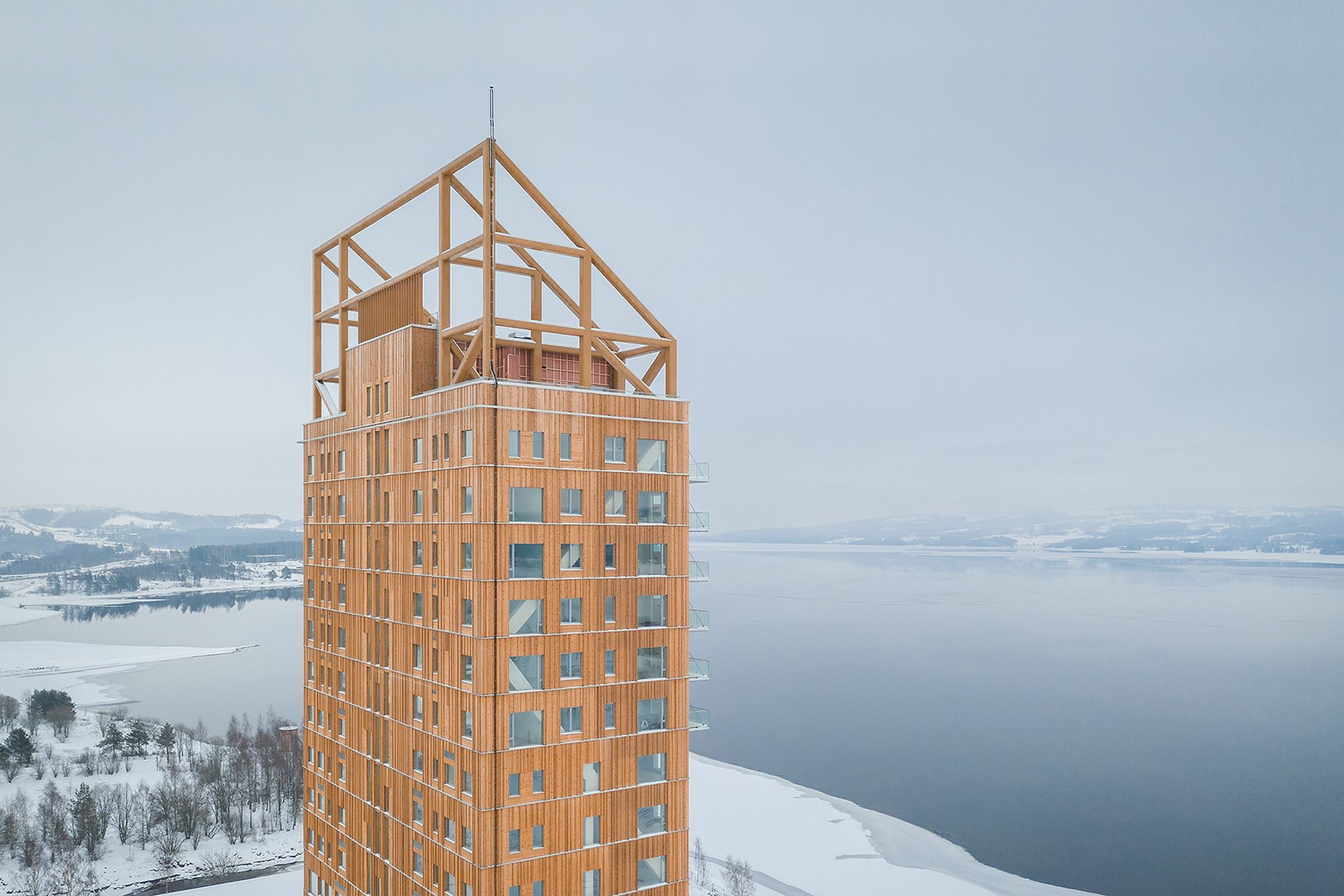
Almost the entire highrise is built from wood. Glue-Laminated Timber (GLT) was used for columns, beams, and diagonals form the primary load bearing system. Staircases and elevator shafts were made from Cross-Laminated Timber (CLT), and the prefabricated facade elements with a wooden cladding, attached outside the timber skeleton, make up the building’s skin. Only from level 12 onwards, concrete slabs provide additional weight and improved dynamics. Engineered wood products (GLT, CLT, LVL) consist of wooden layers glued together in different angles and thicknesses. Depending on the wood’s lifetime, it can be carbon-neutral or even -negative, while the use of adhesives remain an unsolved problem.
Pavilion CIRCL
Amsterdam, Netherlands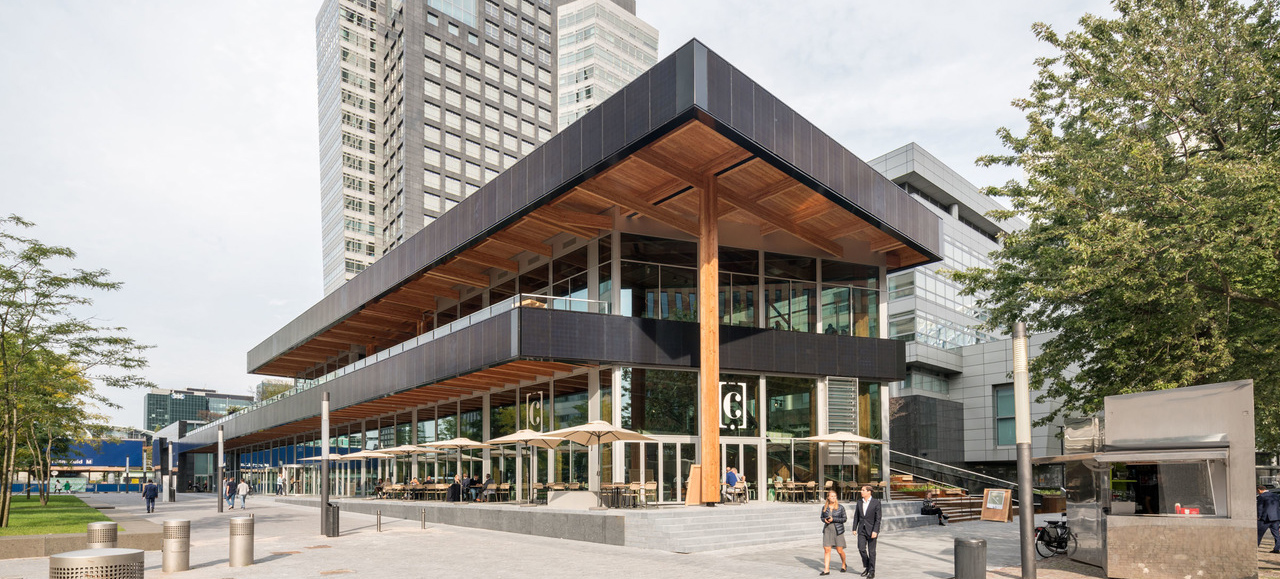
Solar panels create electricity that flows into the local grid, geo-thermal heating coils provide warm water and phase changing materials act as a temperature buffer. The solar panels installed on the roof and walls produce direct current that can be used within the building for charging electronic devices or the LED lights, minimising the need for adapters and inverters that usually change the alternate current from general electricity networks to a direct one. The panels themselves are designed and manufactured in the Netherlands and because of its additional glass layer, they last longer. Underfloor heating, connected horizontally and vertically by coils, heat water naturally and distributes it. The greenery on the roof and facade of the building protects it from sun and the evaporating water from plants cools the city’s climate.
Bombasei Areal
Nanikon, Switzerland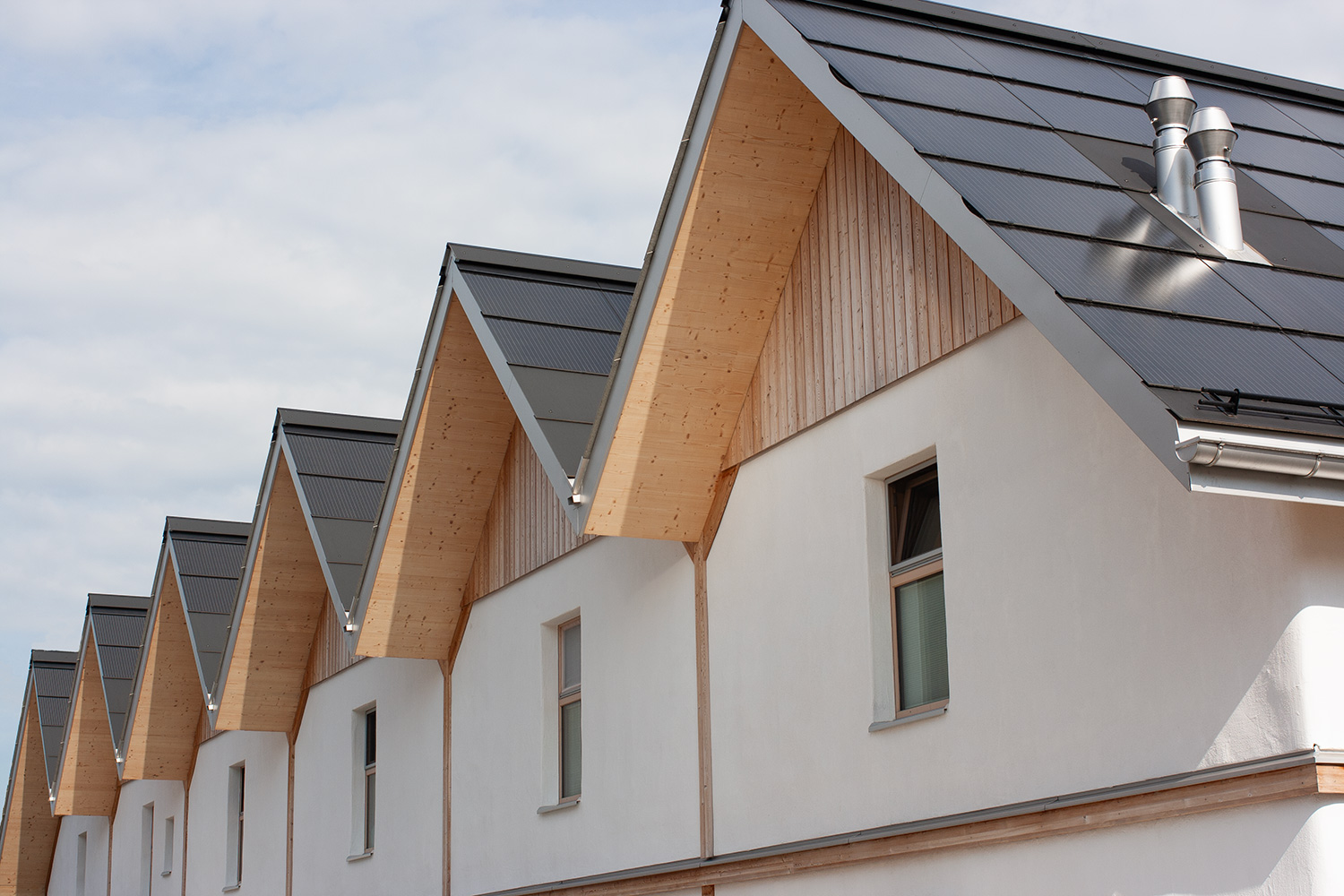
The low-cost straw is an ideal insulating material due to its low thermal conductivity. It also contributes to a good indoor climate. Compared to conventional building materials, some of which are produced in very complex processes, straw bales contain much less grey energy. "Straw accumulates during grain cultivation anyway," explains Paul Schmidt. "By using it as a building material, we are putting an agricultural byproduct in use". A lime plaster protects the straw panels from moisture and provides fire-resistance.
CRCLR
Berlin, Germany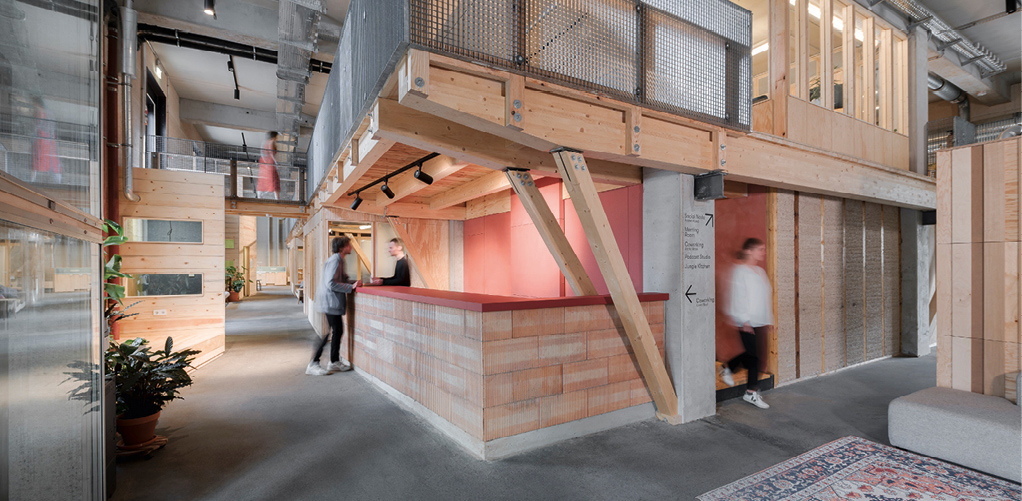
The goal of the initiative was to consciously use sustainable and compostable building materials to enable the resources to be returned to the natural cycle. For instance, the interior insulation of the south facade consists of recyclable or compostable materials such as wood panels, clay plaster, and wood fibre insulation boards. Hemp and clay were used for interior insulation in the window area to seal gaps in the old masonry.
The extension was planned as a timber frame construction to create adaptable spaces. One particular challenge was the fire protection for wooden structures. Despite fire protection requirements R90 and REI90, encapsulation of the load-bearing wooden components was avoided, and the charring behavior was demonstrated. Wood connectors were used to save on construction height and connection materials.
Using a straw bale construction for a passive house suitable external wall was another learning experience. Challenges arose as no company was found willing or able to undertake a project of this scale. Instead, suitable craftsmen were found and trained by experienced members of the FASBA (Fachverband Strohballenbau Deutschland e. V.). The external walls were prefabricated in elements up to 4 meters long and coated with a lime base plaster. The use of a newly developed filler from a clay plaster manufacturer for airtight connections proved promising but is not yet certified. The straw bale construction remains freely accessible for easy leak repairs.
OBK 27
Paris, France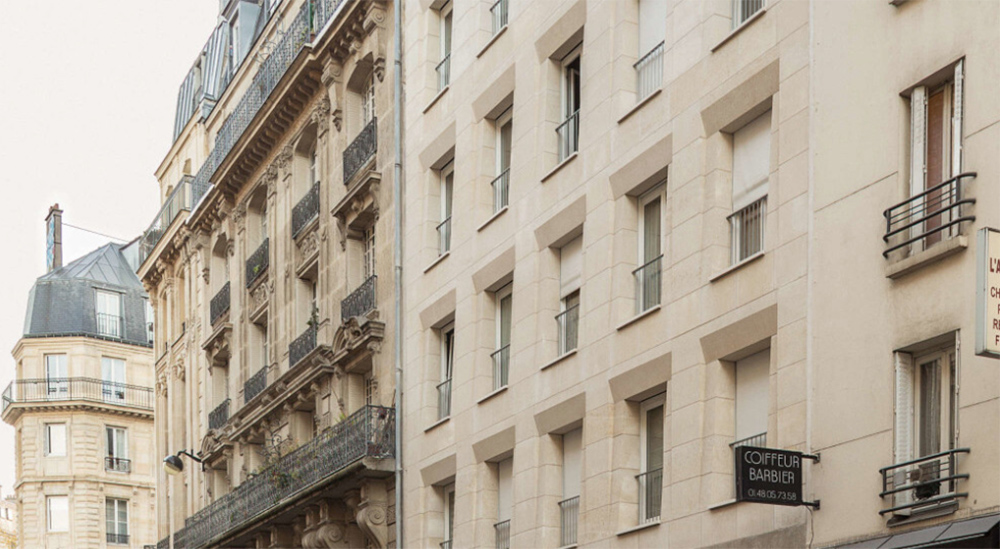
The architects deliberately selected raw materials with minimal transformation and inherently low CO2eq values. As a result, the entire process from extraction and production to transportation and construction becomes carbon negative. The primary material, Brétignac sandstone, requires minimal energy for extraction and cutting. Its emissions primarily stem from the use of fossil fuels during transportation. Natural stone possesses isotropic properties, exceptional durability, and a very slow rate of ageing. It can be used in its natural state without any chemical reactions or transformations. The main minerals composing natural stone, such as quartz, feldspar, and plagioclase, remain unchanged. The massive blocks of natural stone have the remarkable ability to be reused repeatedly. Their durability, isotropic properties, monolithic and homogeneous qualities, and low rate of ageing make them highly suitable for reuse. According to Gilles Perraudin, "if you build a building out of stone, you have a new quarry because you can reuse that stone. Stone can be reused as it is, it doesn't require recycling." Flat bed mortar, a cement-based mortar capable of withstanding high pressure, was used for the joints between the stones. Recognising that the connection between stones is typically the weakest part of stone structures, the load-bearing mortar was protected from the elements on the exterior with a lime-based mortar, which is easier to maintain.