TECLA
Massa Lombarda, Italy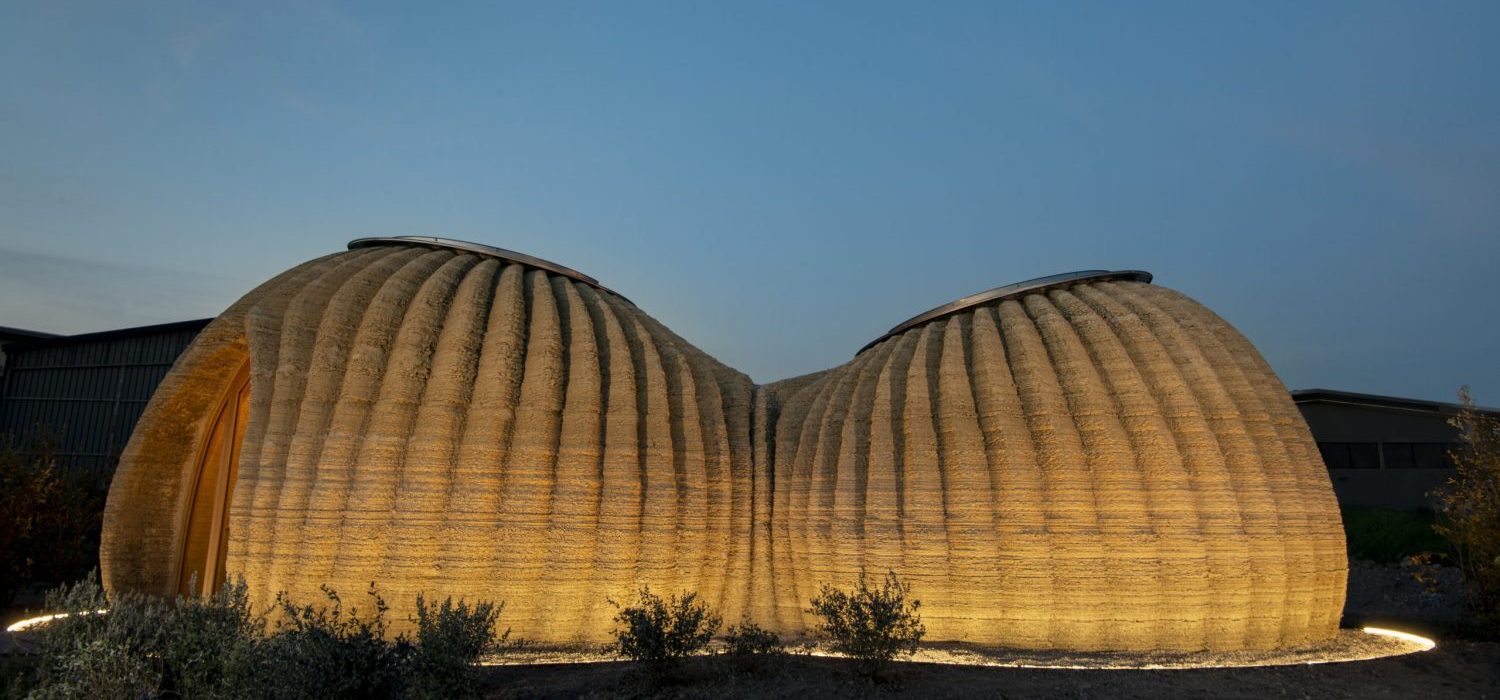
- Construction time
- 2019-2021
- Building type
- Experimental
- Client
- Private
- Architect
- Mario Cucinella Architects
- Project Partners
- Milan Ingegneria (Structural Engineering), Mapei (Earth Science), Capoferri (Windows), Frassinago (Landscaping), RiceHouse (Insulation), Imola Legno (Timber Solutions), Lucifero’s (Lightning), Ariatta (Energy/ comfort consultancy), Primat Terracruda (Earthen floor)
- Size
- 60 m2
- Use
- Housing (Experimental)
- Website
- Link ↗
- Banner image
- Mario Cucinella Architects/Iago Corazza
General description
Tecla (technology+clay) is the first housing project in raw earth realized with 3D printers. This experimental project is located in Ravenna, Italy, and was designed by architect Mario Cucinella in collaboration with WASP, a 3D printing company specialized in earth and clay. In a parametric yet vernacular architectural style, the 60 m² buildings were designed in a pragmatic and simple manner. The two self-supporting earth domes measure 4.2 meters in height and are complemented with a wooden ring and a skylight. The experimental buildings are the result of many years of research, and the development of both the earth mixture and the 3D printing technology is still ongoing. The unique collaboration between the stakeholders involved has made it possible to achieve a shared innovative vision and a high-quality outcome.
WASP takes inspiration from the potter wasp. We build 3D printed houses using earth found on the spot, under a sustainable perspective.
Massimo Moretti, WASP founder
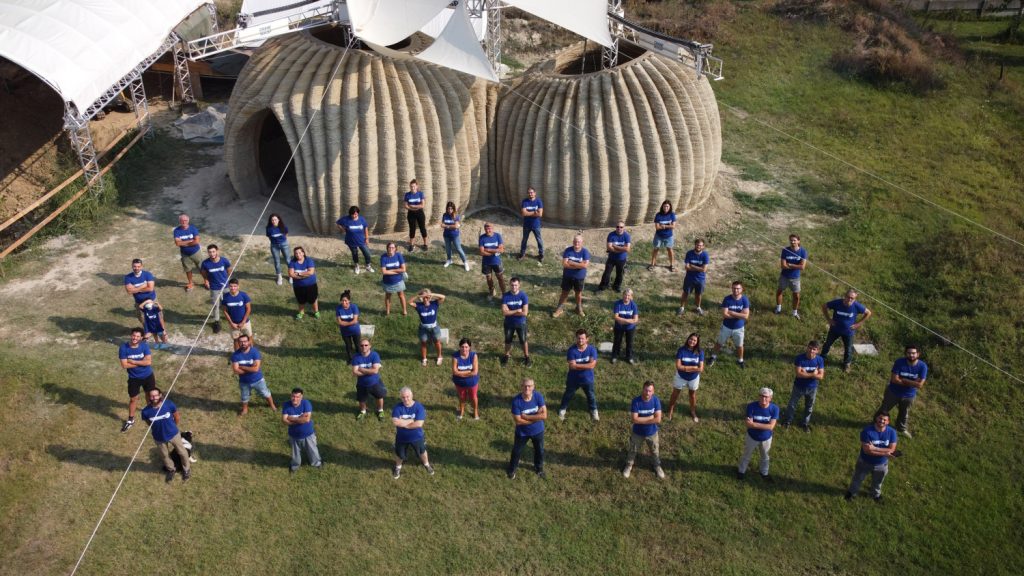
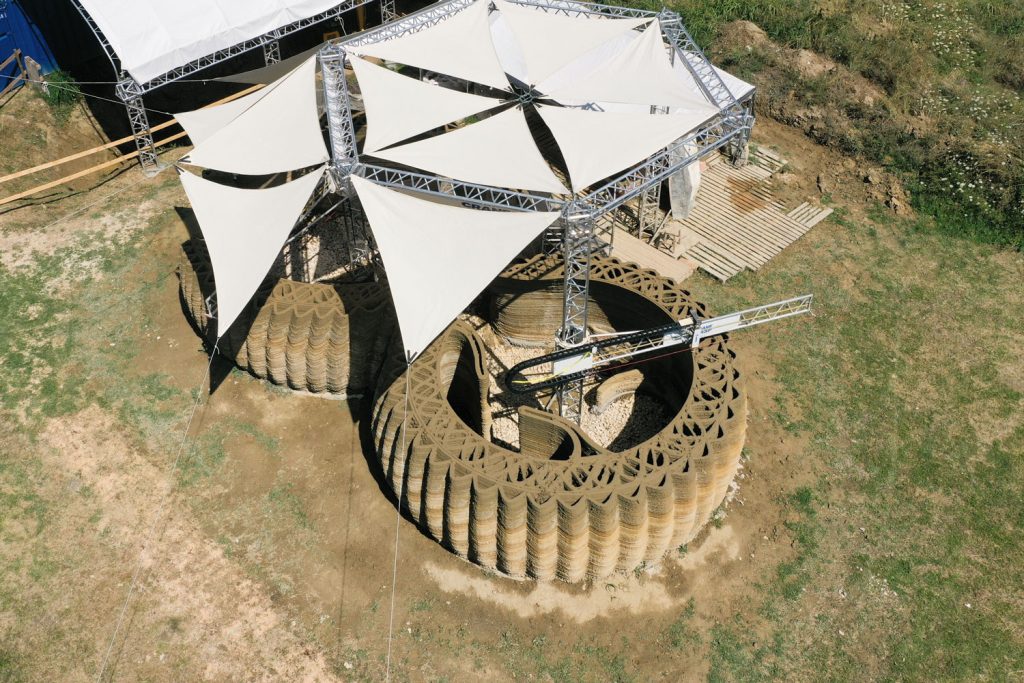
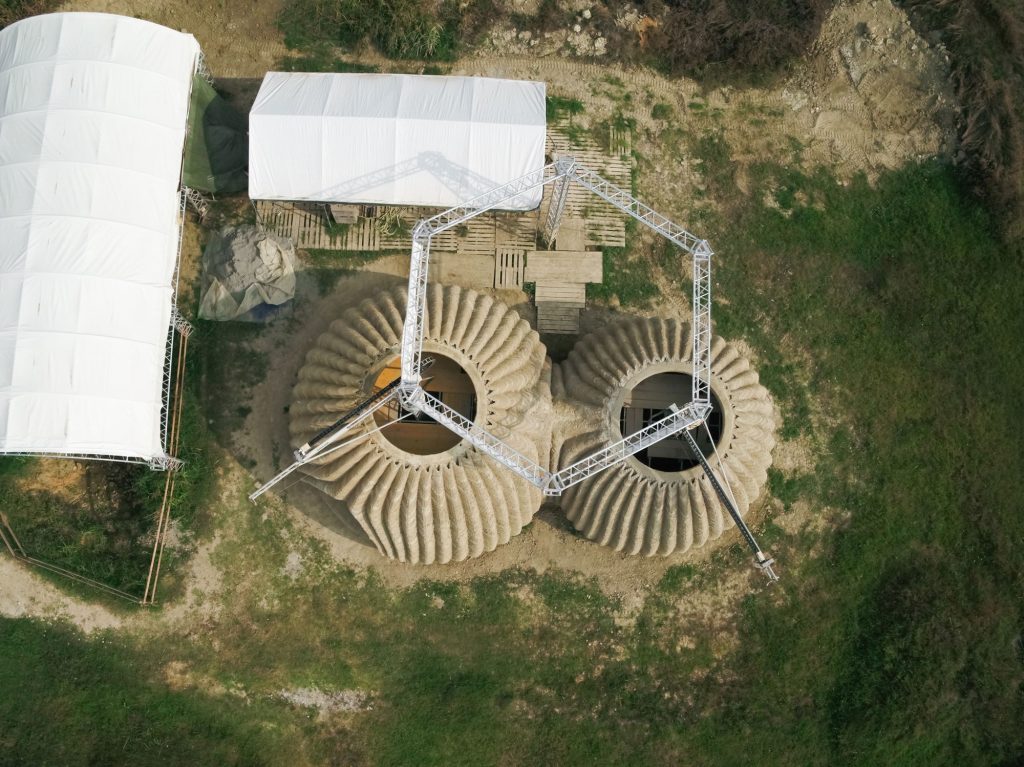
Introduction to Circularity
The project places a strong emphasis on achieving high levels of circularity and sustainability by selecting materials primarily from renewable bio-based sources. This includes the composition of the walls, insulation, and foundation. Concrete was intentionally not used in the construction. Instead, a gravel foundation was chosen to enhance circularity and eliminate embodied carbon typically associated with concrete foundations. However, it’s worth noting that gravel production often involves crushing high-quality rock. The construction method employed is highly automated, requiring minimal labor and only a few workers, which contributes to the structure’s remarkably low cost for an earth-based project. Furthermore, the assembly of the structure is designed to facilitate disassembly if needed in the future.
TECLA shows that a beautiful, healthy, and sustainable home can be built by a machine, giving the essential information to the local raw material.
Massimo Moretti, WASP founder
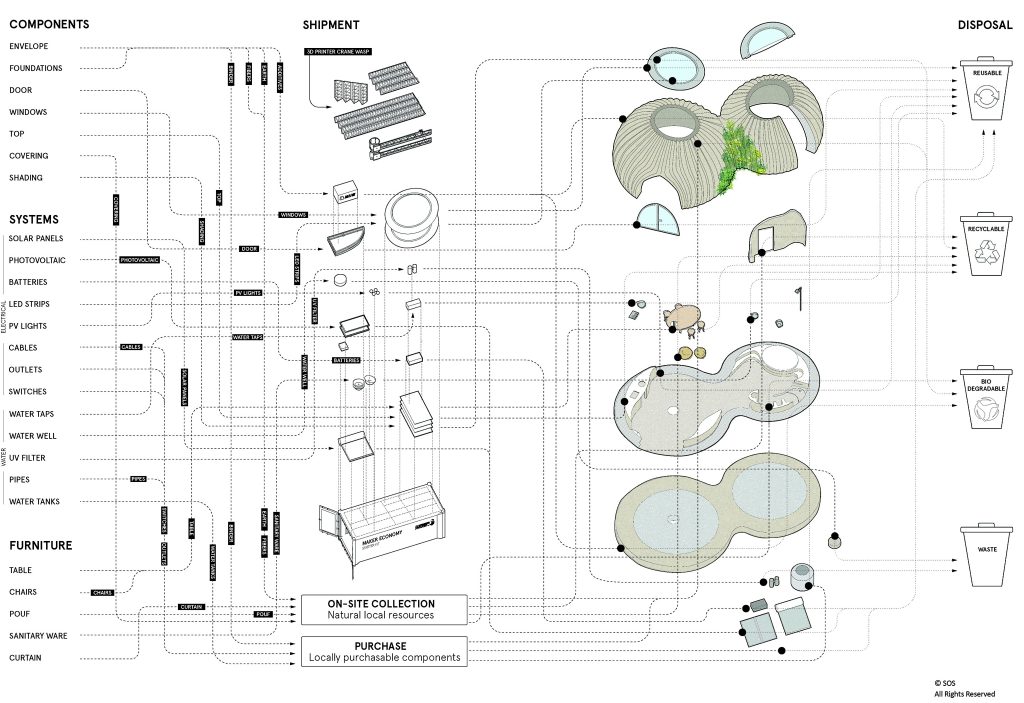
Practices
I think the revolution of 3D printing is to give people a degree of freedom in how to do things, without being connected to a big professional industry.
Mario Cucinella, Architect
The completion of the structure is an important milestone and shows that, thanks to the design and technologies used, TECLA is no longer just a theoretical idea but can be a real and achievable response to the needs of living today and the future, that can be declined in different contexts and latitudes.
Mario Cucinella, Architect
The soil used for construction was obtained from the site, analysed, and mixed with additives. Using a 3D printing technique, a total of 350 layers consisting of sinusoidal and continuous lines were printed within a time span of 200 hours. After a drying period of approximately 3 months, the structure was fully formed. The load-bearing earth walls eliminate the need for additional framing construction. To ensure effective insulation, the wall cavities were filled with rice husk obtained from agricultural waste.
The foundation is composed of three consecutive layers of rammed earth, rice husks, and gravel. The furniture is integrated into the structure and also printed, with only a few non-printable parts sourced from Italy. In order to improve the printability and structural qualities of raw earth, other materials were mixed in. Since soil composition varies, the mix was enhanced with silica sand, which accounts for 19% of the mixture. Additionally, shredded rice husks were added to increase longevity and help bind the earth mixture on a microscopic level.
However, a significant tradeoff was made, as approximately 10% of the earth mixture by weight consists of binders (4.69% lime and 4.7% hydraulic lime). Binders cannot be considered circular or sustainable, as their production involves the downcycling of stone while emitting high amounts of CO2. Binders only exhibit their binding effect once, during their chemical reaction. In reuse, they lose their binding function and behave like any other grain. Consequently, a new binder is required for each recycling process. Furthermore, binders are produced by quarrying rock or marl, which is pulverised and then burned. Often, high-quality rocks such as limestone are reduced to powder that can only be used once, resulting in relatively low-quality materials with limited durability and strength.
62% of the material used in the project is derived from renewable bio-based sources. Rice husk, the outer shell of rice, is utilised as insulation material for both the building’s envelope and floor. Typically, rice husks are discarded as waste, but in this project, they have been repurposed into a building material, thereby reducing the CO2 footprint associated with rice husks. Normally, rice husks are either burned in fields or left to decompose, contributing to environmental emissions.
With the advancement of modern technology, the automation of labour-intensive processes has become possible, potentially changing the economics of earth structures. WASP, leveraging their experience in small and mid-scale 3D printing, has developed Crane Wasp, a modular printer system with a build area of 50 m2, starting at a price of €132,000. In the construction of Tecla, two printing arms were synchronised to lay each of the 350 12mm lines. Although the printing process took only 200 hours to complete, the earth mixture had to dry for approximately 3 months due to the use of binders.
During this drying period, the printer can be moved and used to print another building, making this technology highly cost-effective. It is conceivable that a set of printers could construct 20 personalised houses, each with its own design, within a year with only a few workers. 3D printing is often regarded as a straightforward way to automate construction processes, but it still requires specialists who can troubleshoot the technology in the event of breakdowns or inconsistent results.
Material inventory and supply chains
The soil used for the project is sourced directly from the site, where the excavation has transformed into a pond, resulting in a unique outcome of material extraction at a distance of 0 kilometers. Rice husk, another key material, is obtained from various locations across Italy where rice is grown and processed. Lime and hydraulic lime, which are globally available materials, are produced at multiple sites throughout Italy using raw materials such as limestone or marl sourced from different regions in the country. It is likely that the lime and hydraulic lime used in the project are sourced within a radius of approximately 200 kilometers. Gravel, often produced by crushing granite, is a commonly used material sourced globally. In the case of this project, it is likely sourced within a range of 300 kilometers from the project site. Overall, approximately 60% of the project’s materials originate from the site itself, while the remaining materials are sourced from various locations within Italy, all within a radius of less than 400 kilometers from the site.
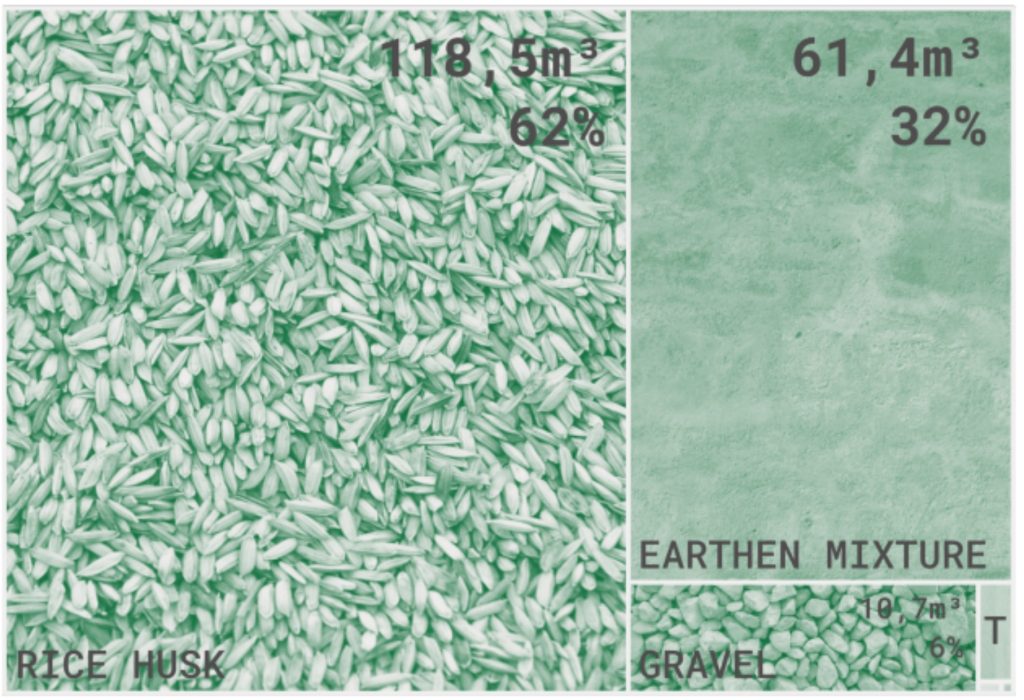
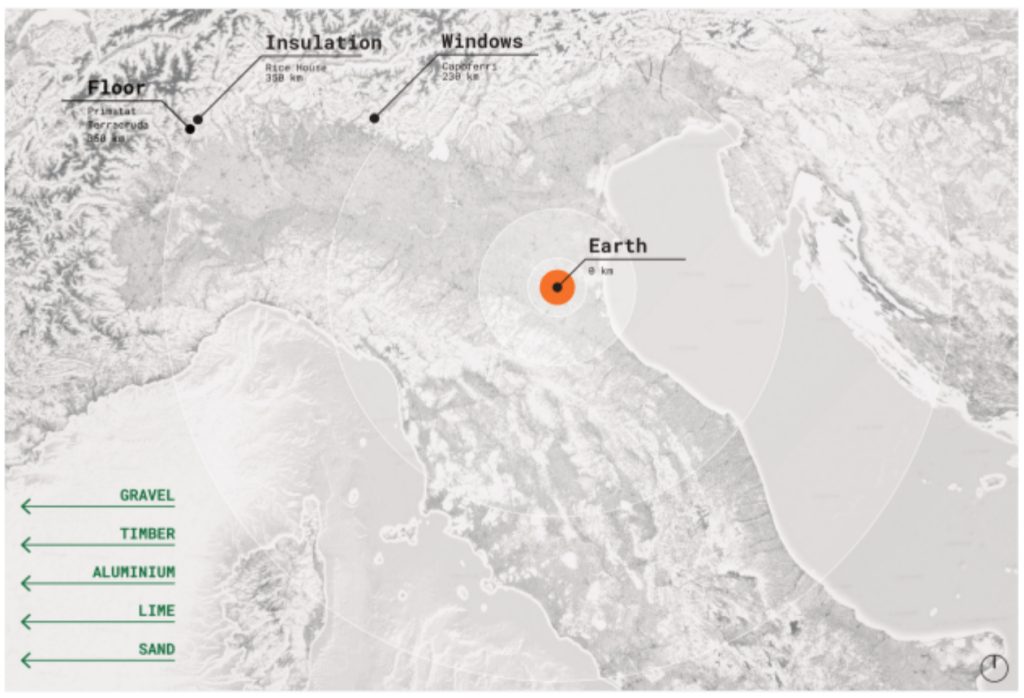