THE EDGE SÜDKREUZ
Berlin, Germany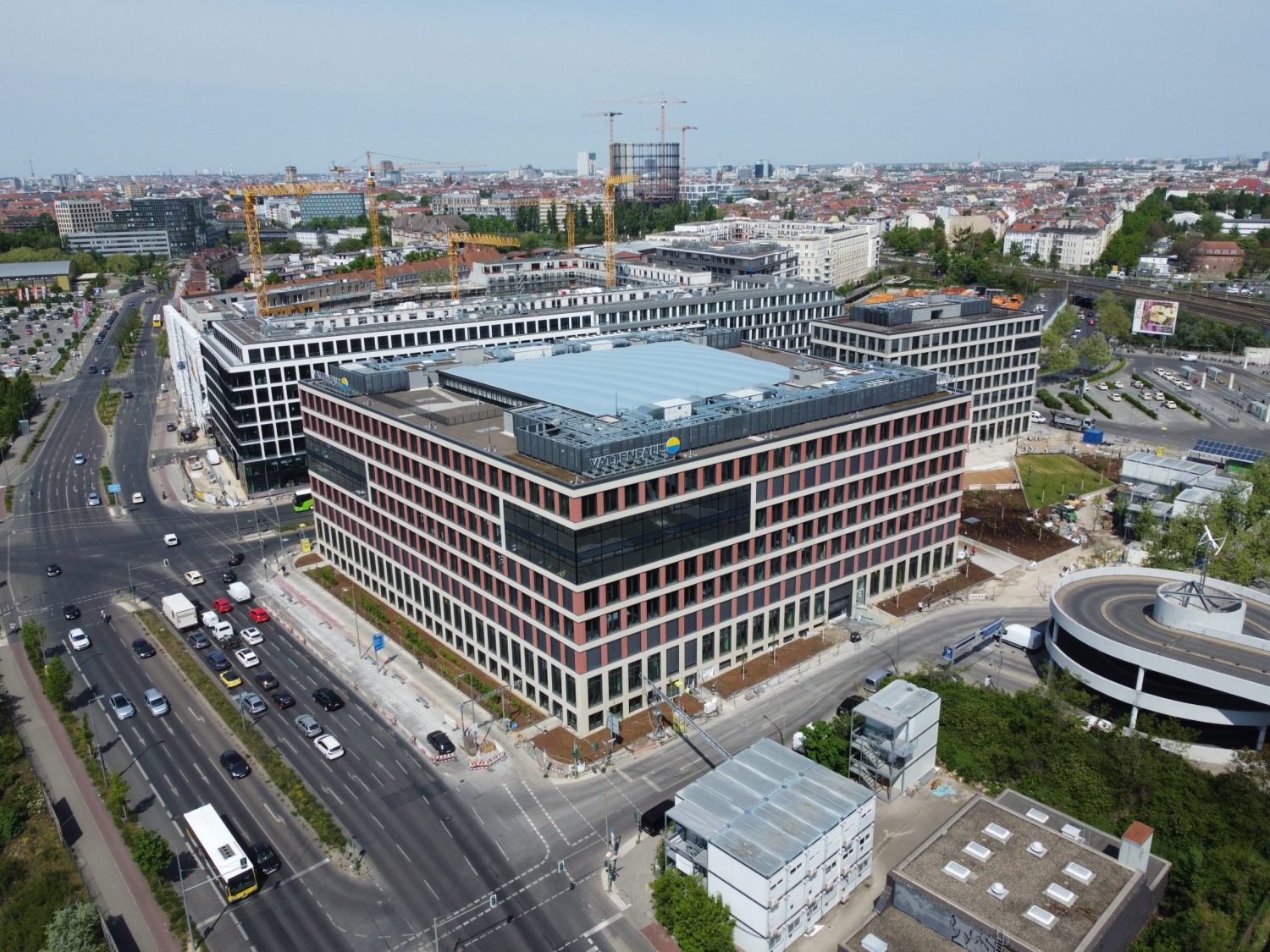
- Construction time
- 2019-2023
- Building type
- New built
- Client
- EDGE
- User
- Vattenfall
- Architect
- Tchoban Voss Architekten
- Project Partners
- CREE Deutschland, Rhomberg Systemholzbau, Buro Happold (Structural engineering, building services, sustainability consulting and certification), de Winder Architekten (interior architecture); SMV Bauprojektsteuerung Ingenieurgesellschaft (project management), hochC Landschaftsarchitektur (landscape architecture), Arup Deutschland (facade)
- Size
- 32.000m2
- Use
- Offices
- Website
- Link ↗
- Banner image
General description
The EDGE Südkreuz is a hybrid office building that serves as the new German headquarters for the company Vattenfall. It accommodates approximately 1,200 people on a daily basis. This six-story building includes a basement with underground parking and a spacious ground floor featuring tree-like stairs that ascend upwards. Each “tree” incorporates platforms that encourage encounters and interactions among individuals. Situated in close proximity to a major train station, the building offers convenient accessibility for its users. Additionally, it has established a comprehensive e-mobility charging infrastructure to support the charging needs of the company-owned vehicles.
When we released the plans of building with wood, everyone was happy. A Problem was that everything took twice as much time because no one had done it before at such a scale.
Anja Borchard, Project Management
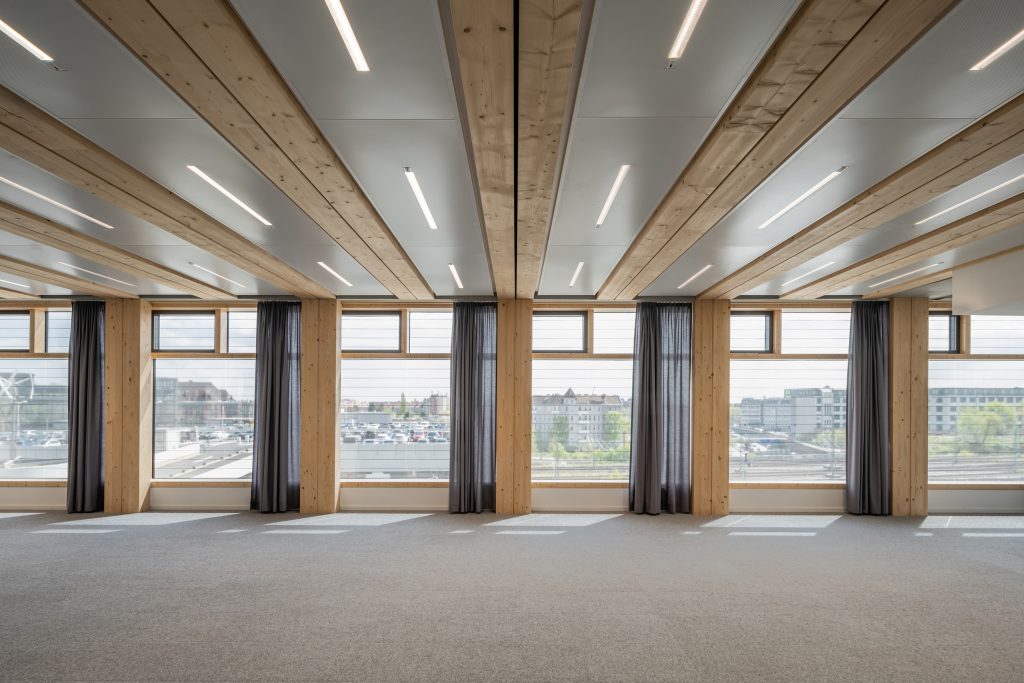
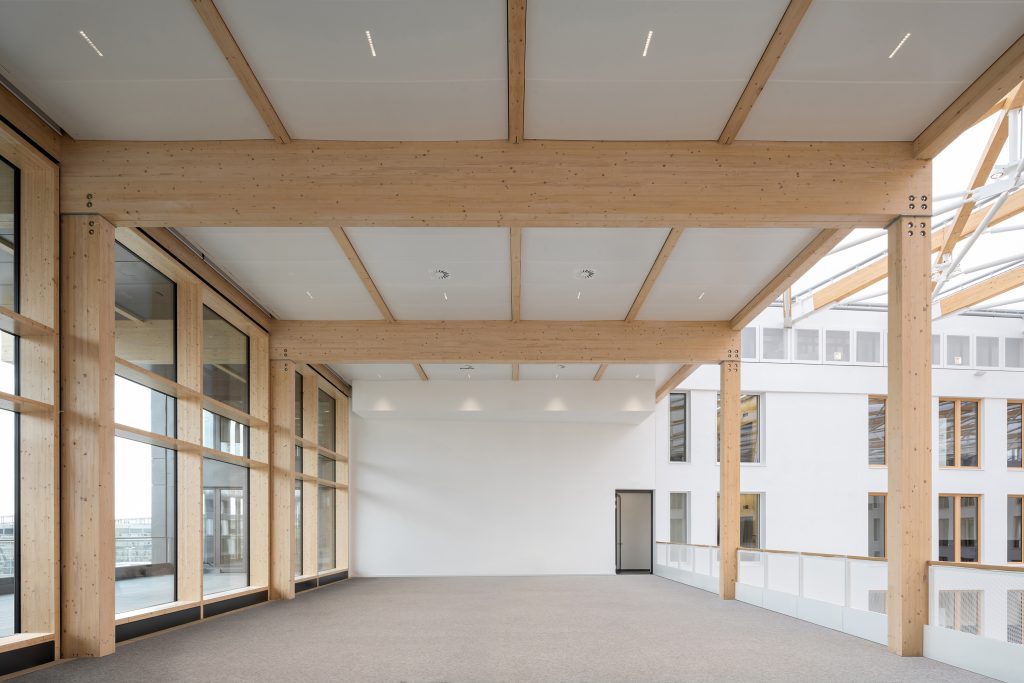

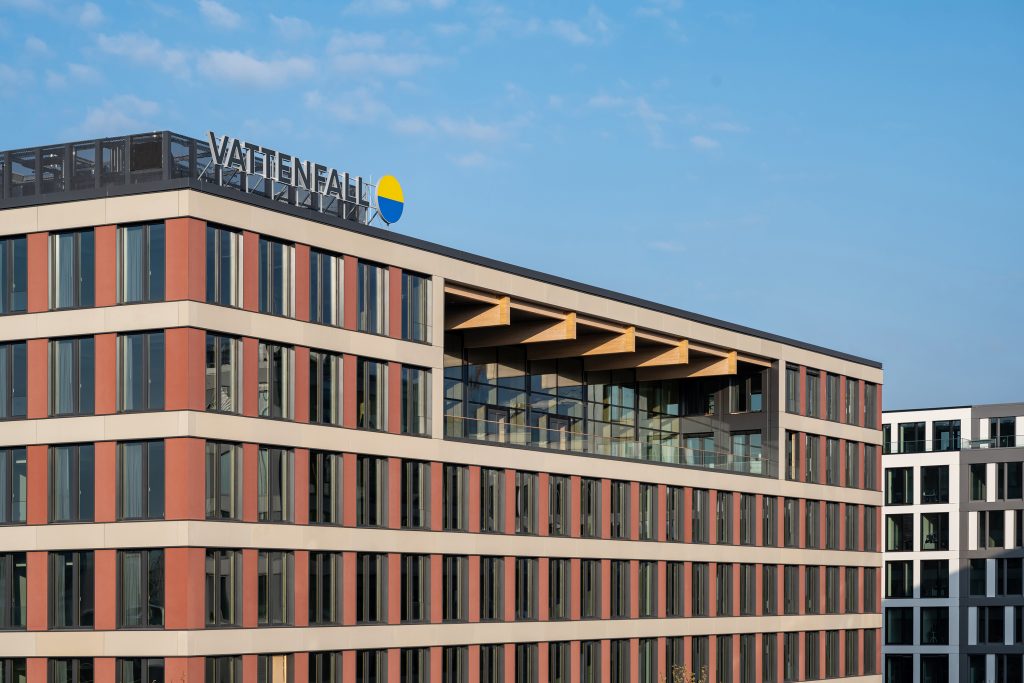
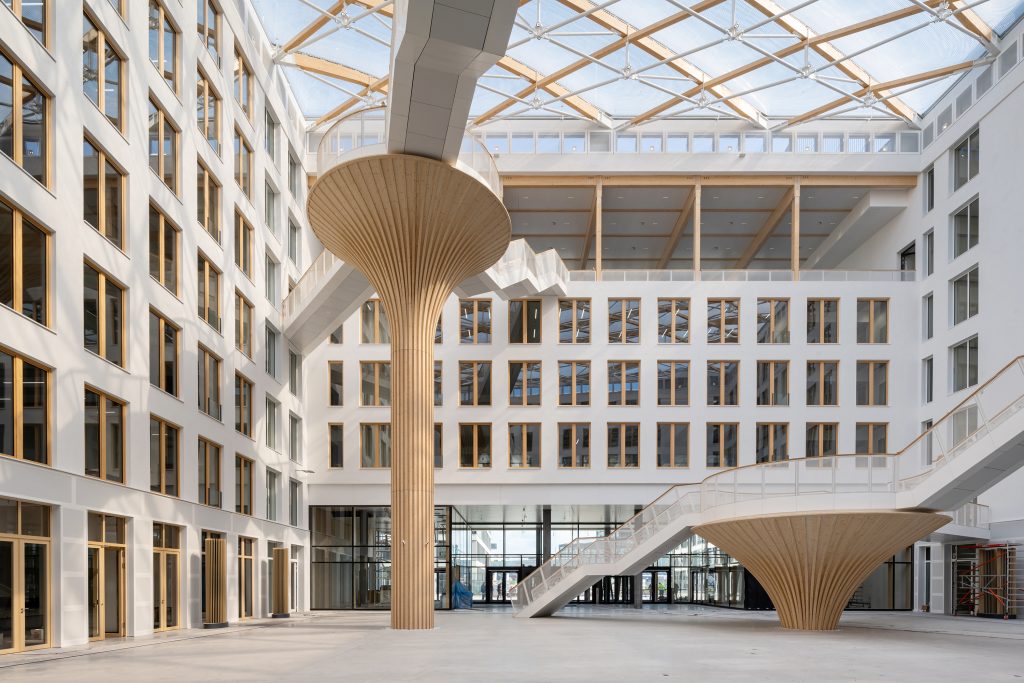
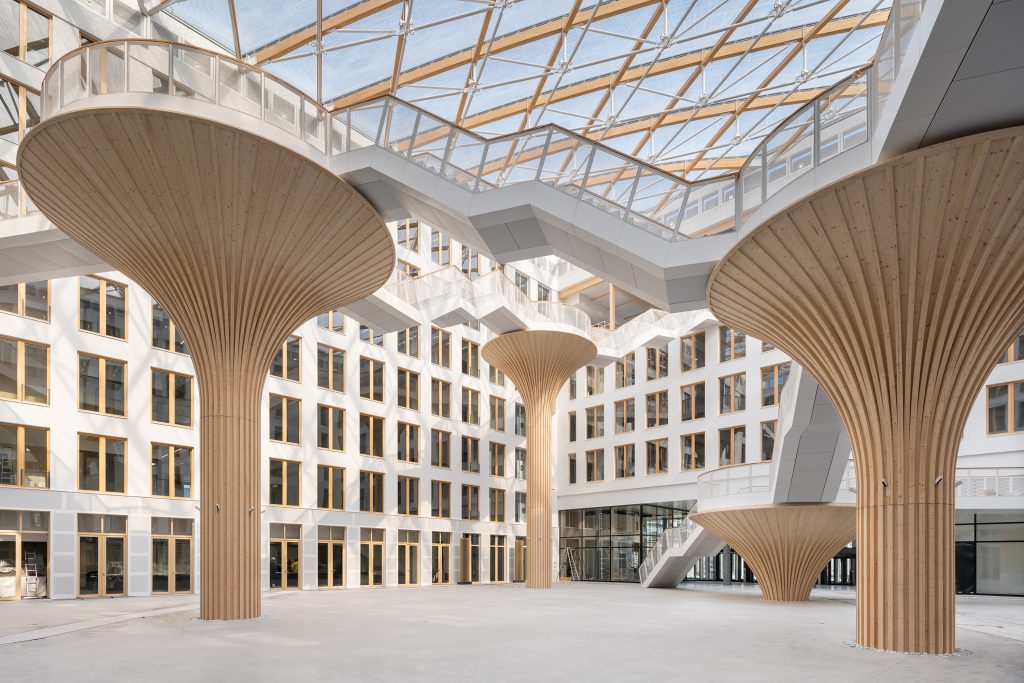
Introduction to Circularity
The modular wood hybrid design of the building combines wood and concrete, resulting in a significant reduction in CO2 emissions compared to conventional buildings. The materials used are assumed to be recyclable, and the use of concrete was minimized wherever possible. The incorporation of wood modules and beams throughout the building is a key aspect of promoting circularity. The design principle is centered around ensuring the building’s longevity, allowing for easy exchange, disassembly, or dismantling of wood modules or beams if necessary, without significant complications. Moreover, the building relies primarily on locally produced bio-methane for heating and water boiling, reducing dependence on other forms of energy.
Practices
The biggest challenges were on the one hand that the building only had one corner with a 90 degree angle and therefore it was hard to plan the modular system and on the other hand the preparation for construction was difficult since the big parts for the modular system needed to be stored on site.
Anja Borchard , Project Management
The project was initially conceived as a conventional reinforced concrete office structure. However, as the developers and architects explored the concept of modularity and integration of a grid system, they came across a modular wood manufacturer that offered a suitable system for the building.
One of the major challenges faced during the construction was managing the space and timing on the site. Unlike traditional concrete constructions, which are less space-intensive during pouring, the arrival of long wooden beams and individual facade panels required careful management of both space and construction schedules.
Logistics and just-in-time delivery of parts were significant challenges due to the scale of the project. To address the logistics, plans were made to transport the beams and other construction materials to the site by train, taking advantage of the proximity to a large railway station. However, a hurdle emerged as there were insufficient railway tracks to support this transportation method.
The structure of the building primarily consists of wood, with the exception of the cores, which remained in concrete due to regulations. All the forces, both horizontal and vertical, are carried by large wooden beams. A key aspect of constructing a sustainable building with wood is ensuring that the timber is sourced from certified plantations.
Material inventory and supply chains
To reduce CO2 emissions, the builder aimed to source materials from within a maximum radius of 500 km. Initially, a forestry in the Czech Republic was considered, as the structural properties of the wood were suitable. However, the surface quality did not meet the requirements, so alternative sources were sought in Sweden. Short supply chains played a crucial role in this process. For instance, the initial processing of the timber and the manufacturing of modules were carried out in geographically close locations, ensuring efficiency and minimizing transportation distances.
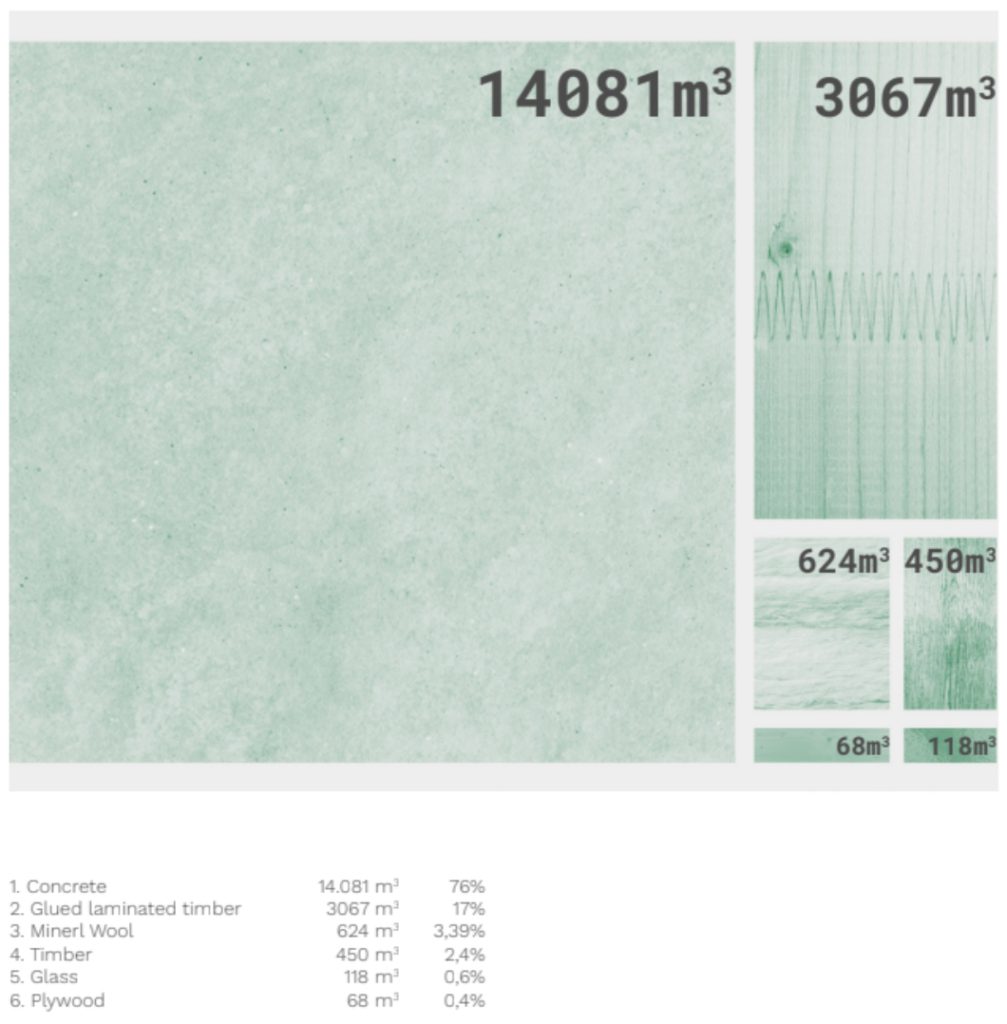
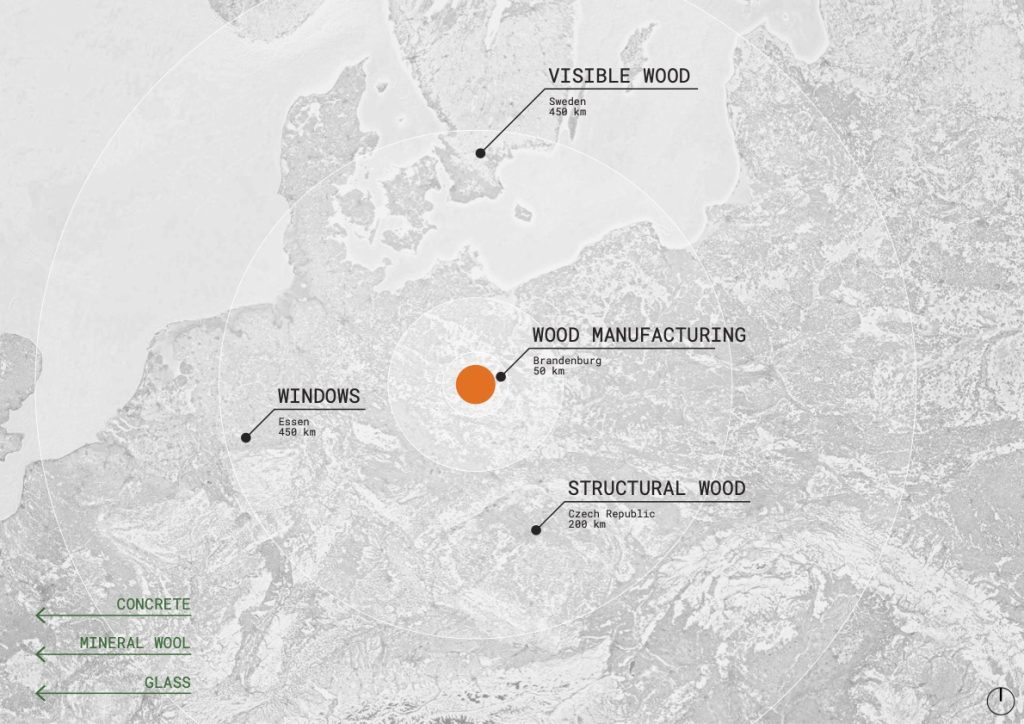