Mjøstårnet
Brumunddal, Norway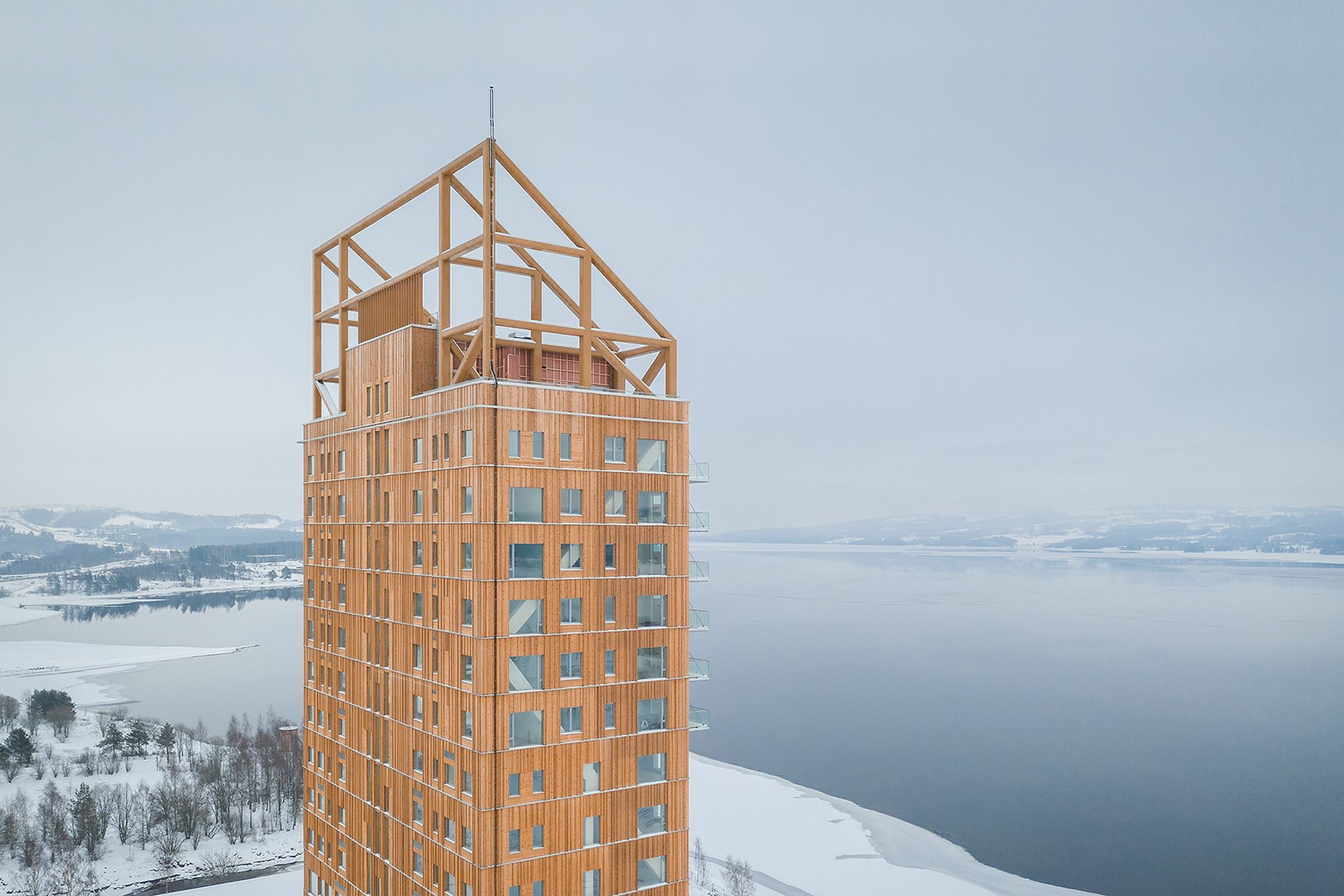
- Time
- 2017 - 2019
- Building type
- New built
- Client
- AB Invest AS (Arthur Buchardt)
- Architect
- Voll Arkitekter AS
- Project Partners
- Hent AS ,Moelven Limtre AS, Sweco Norge AS, Woodcon AS + Stora Enso AB, Metsä Wood, RVTAS, Woodify AS , Norsk Stål AS , Gunnar Hippe AS, Celsa Steel Service AS, Con-Form Norge AS, BetongØst AS, Lian Vinduer AS, Profilteam AS, and others
- Size
- 10500 m2
- Use
- Mixed use (hotel, restaurant, housing, offices, swimming hall)
- Website
- Link ↗
- Banner image
- Vjus AS
General description
At the shore of Norway’s largest lake, Mjøstårnet rises 85.4 metres above the surrounding landscape. It is located in Brumunddal, a small town about 100 km north of Oslo. When it opened in 2019 after a two-year construction period, Mjøstårnet was awarded the world’s highest all-timber building. The 18-storey tower houses a hotel, a restaurant, offices, apartments, a public rooftop terrace, and a swimming hall. Many local companies and suppliers were involved in the project and tried to predominantly use local resources with a clear focus on timber.
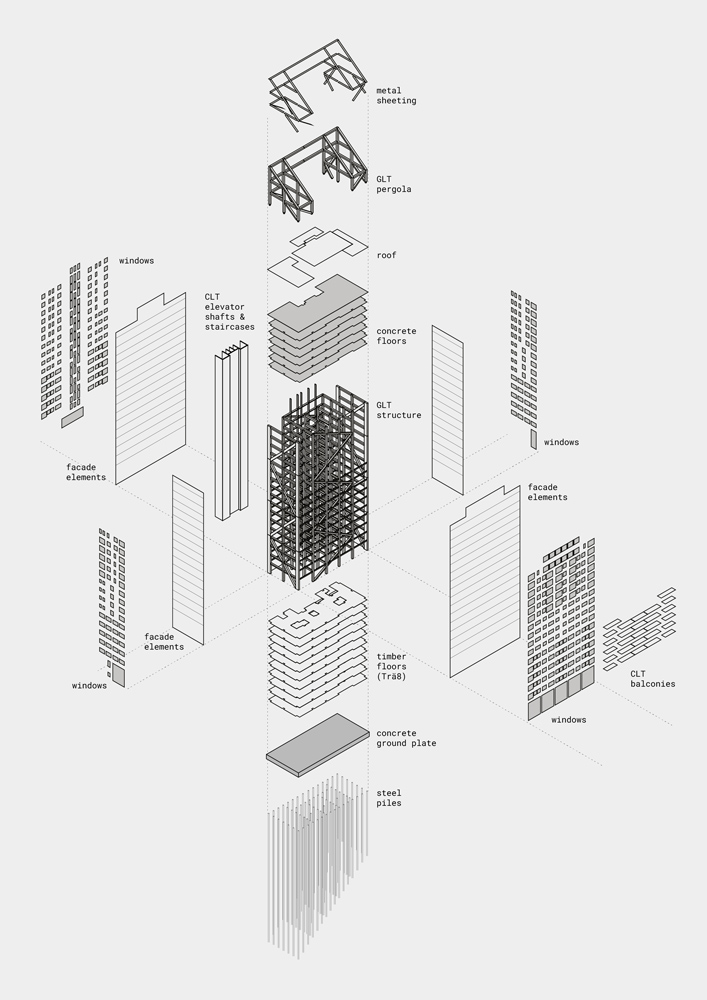
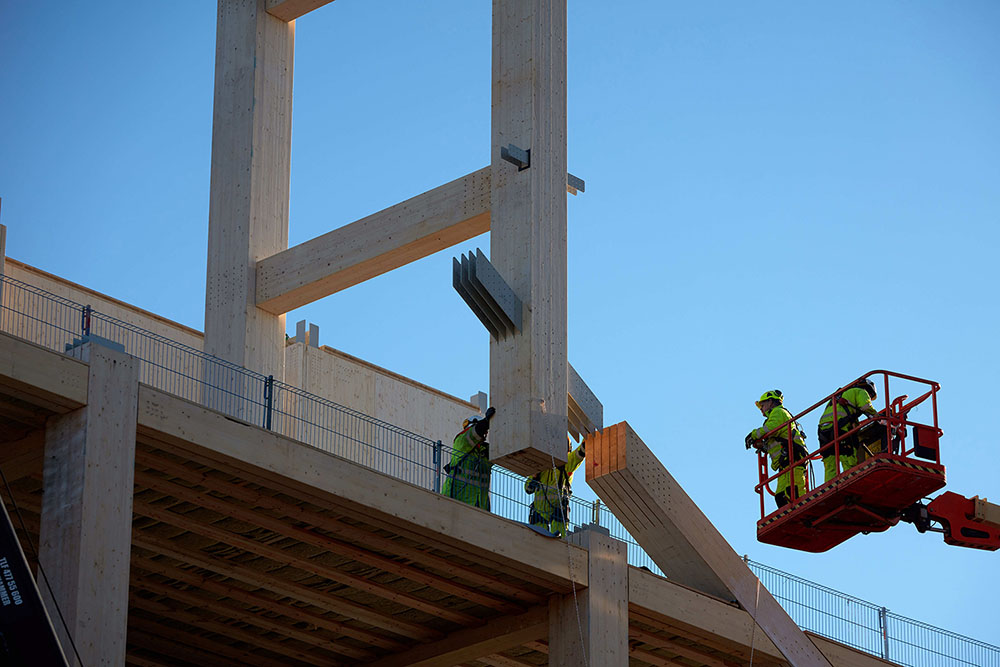
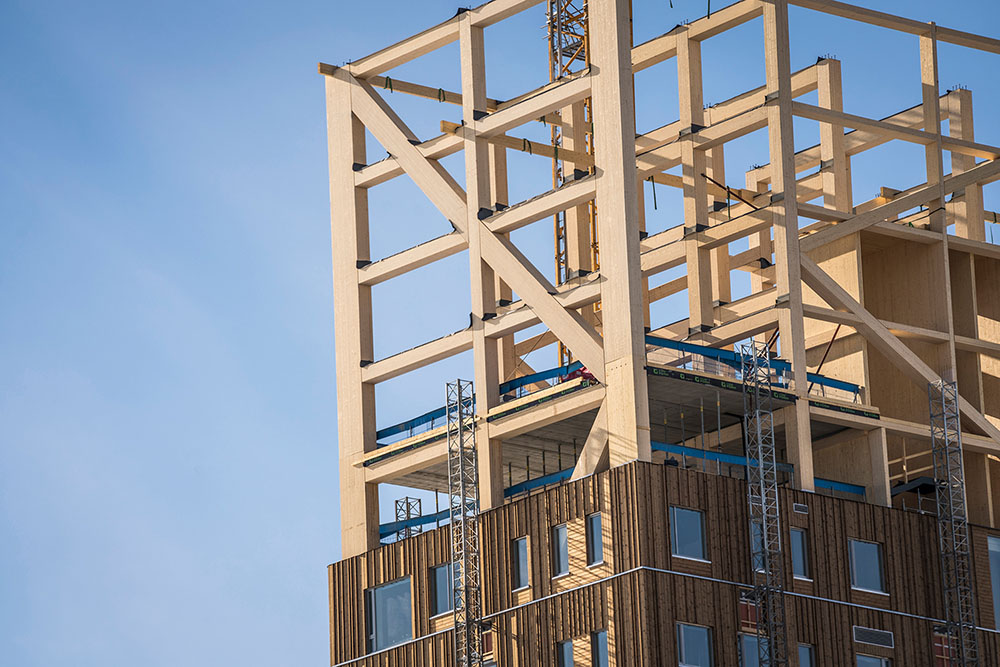
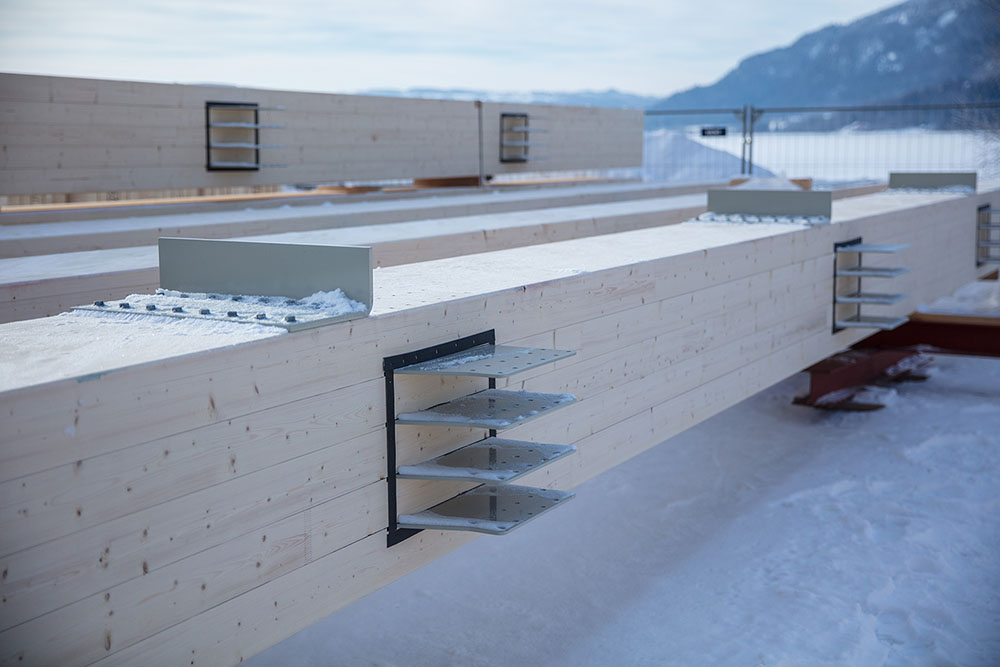
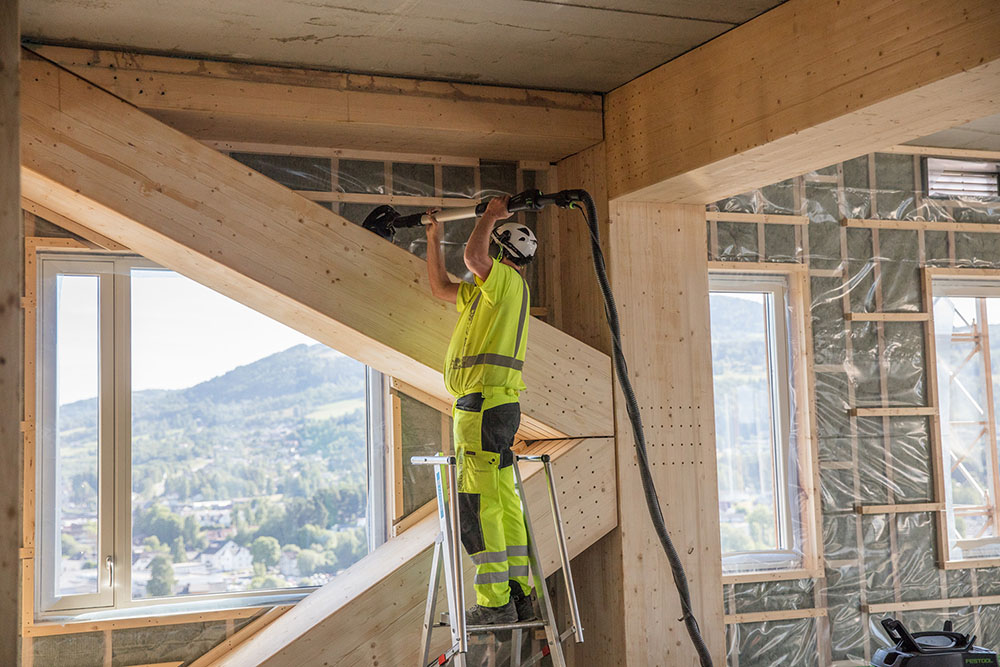
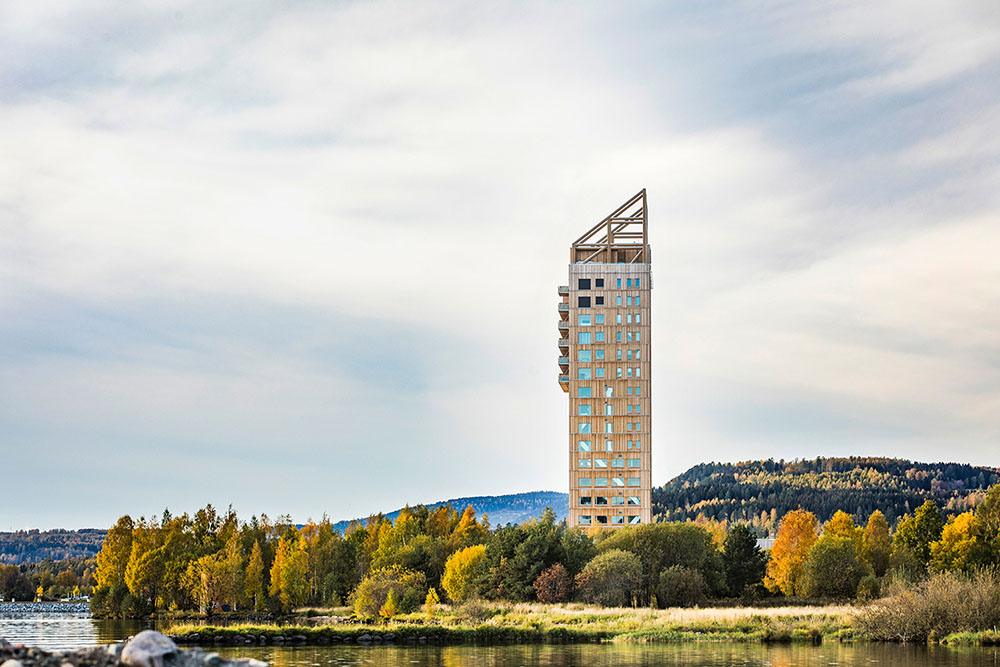
Introduction to Circularity
The most important systemic circular potential of the project is the factor of locality: many materials and much of the know-how come from the region of Brumunddal. Strengthening local economies, working closely with local authorities, improving local knowledge, and shortening transport routes were some of the interlinked benefits. But, Mjøstårnet is not completely detached from the globalised economy, its Cross Laminated Timber (CLT) was produced in Austria. Two materials are particularly interesting in terms of circularity: engineered wood products (GLT, CLT, LVL) and steel as a necessary structural material that is difficult to replace for a building of this height. The latter was produced using a sustainable method, which significantly reduced its environmental impact. At the design level, modular approaches as well as simple construction principles in combination with a joining technology allowing for disassembly, contribute to a potential second life of the materials. However, the main focus of the project was on the long-term preservation of the building.
Building a building like this is a giant IKEA furniture.
Rune Abrahamsen
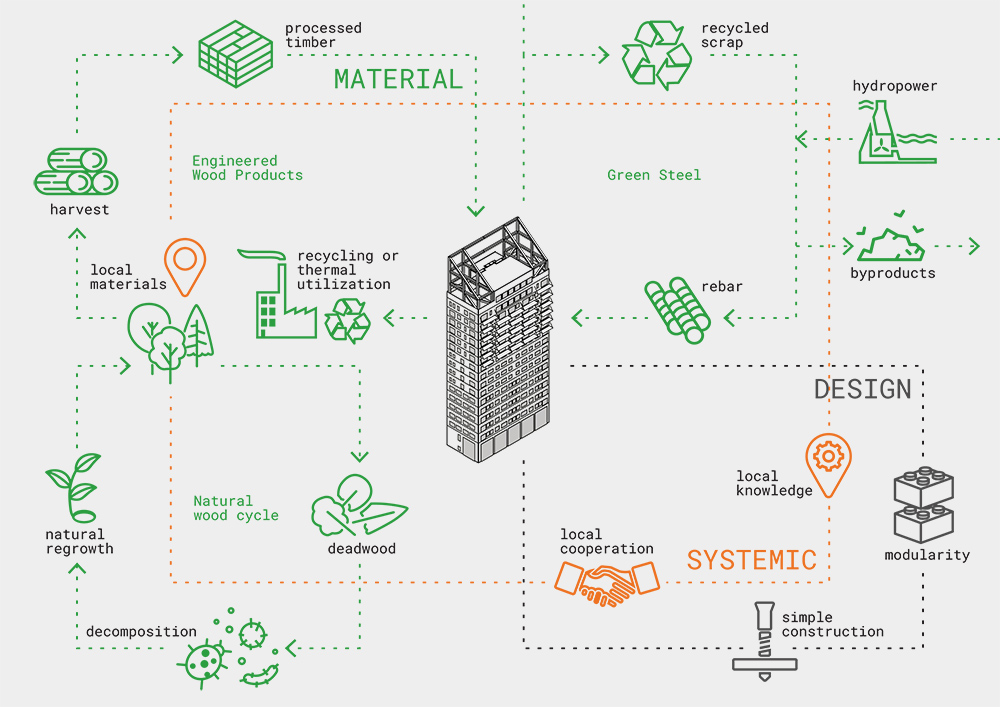
Practices
We should build more tall or high-rise timber buildings in urban areas in the future.
Rune Abrahamsen, CEO of Moelven Limtre AS, Interview Jan. 2022
Building Mjøstårnet wouldn’t have been possible without its joining technology holding together the structural glulam skeleton of columns, beams, and diagonals. The joining technique is based on steel plates, which are slotted into timber elements and connected with screws or dowels. Mjøstårnet’s primary load bearing system consists of GLT columns, beams, and diagonals that were produced by Moelven Limtre in their nearby production site. Every piece was prefabricated in the exact dimensions and directly assembled on site. Only one diagonal did not fit and had to be replaced.
Almost the entire highrise is built from wood. Glue-Laminated Timber (GLT) was used for columns, beams, and diagonals form the primary load bearing system. Staircases and elevator shafts were made from Cross-Laminated Timber (CLT), and the prefabricated facade elements with a wooden cladding, attached outside the timber skeleton, make up the building’s skin. Only from level 12 onwards, concrete slabs provide additional weight and improved dynamics. Engineered wood products (GLT, CLT, LVL) consist of wooden layers glued together in different angles and thicknesses. Depending on the wood’s lifetime, it can be carbon-neutral or even -negative, while the use of adhesives remain an unsolved problem.
Mjøstårnet was a project without preassembly, which saved a lot of time and costs. The timber skeleton was built in steps of self-stabilising units of four to five stories. When eight stories were installed, the facade contractor started attaching the facade elements. For the construction, a tower crane and additional mobile cranes and lifts, but no external scaffolding was needed. The total cost of Mjøstårnet was only 2 – 3 % higher than the costs of a conventional building. Another approach that contributed to the cost saving aspect was the close cooperation with the local authorities who supported the timber development. As a result, the building permission process was accelerated.
Material inventory and supply chains
GLT was used for the primary load bearing structure and as the most characteristic material of the project, it was sourced and processed in the region of Brumunddal. The prefabricated elements, the glass facade and the cast concrete come from production facilities in the immediate surroundings. Further production sites are mainly located in Scandinavia, such as for reinforced concrete, steel elements, precast concrete, and windows that were all produced in Norway, Thermowood was produced in Sweden, and LVL was produced in Finland. The CLT was produced in Austria.
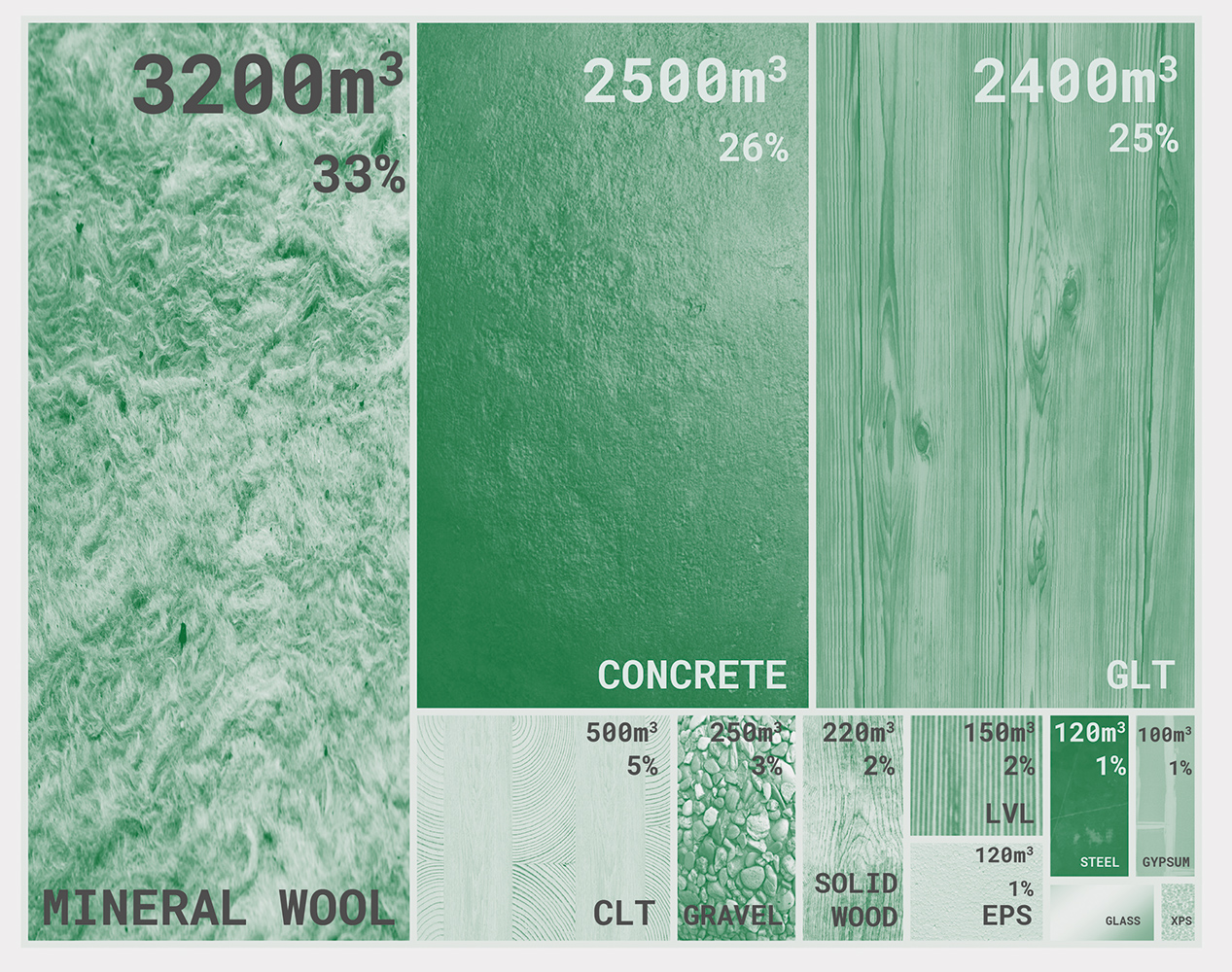
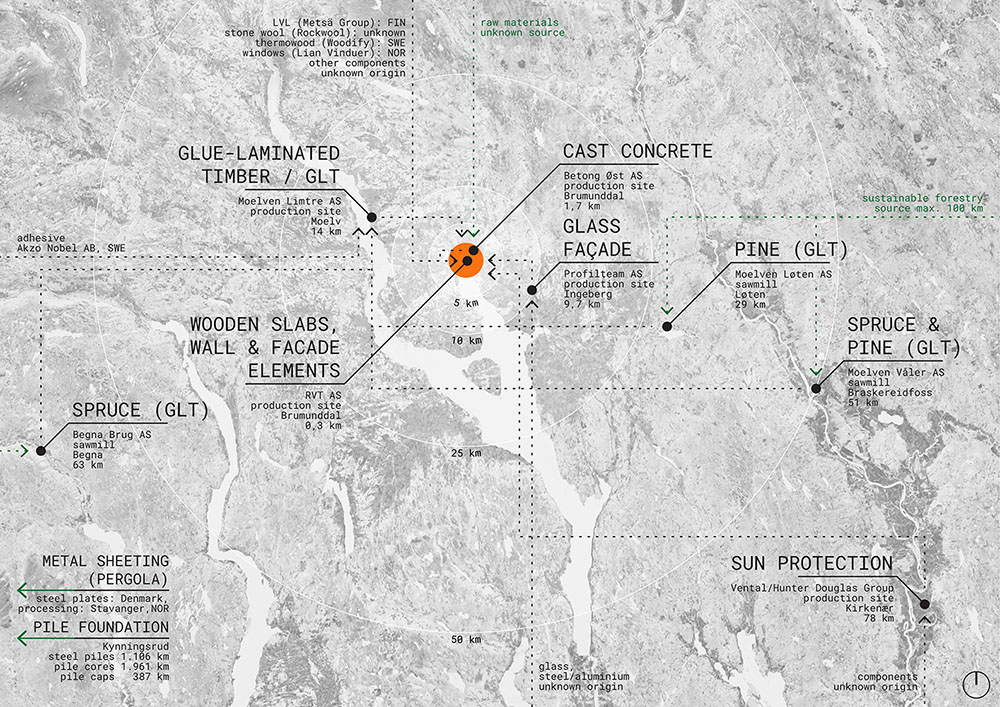
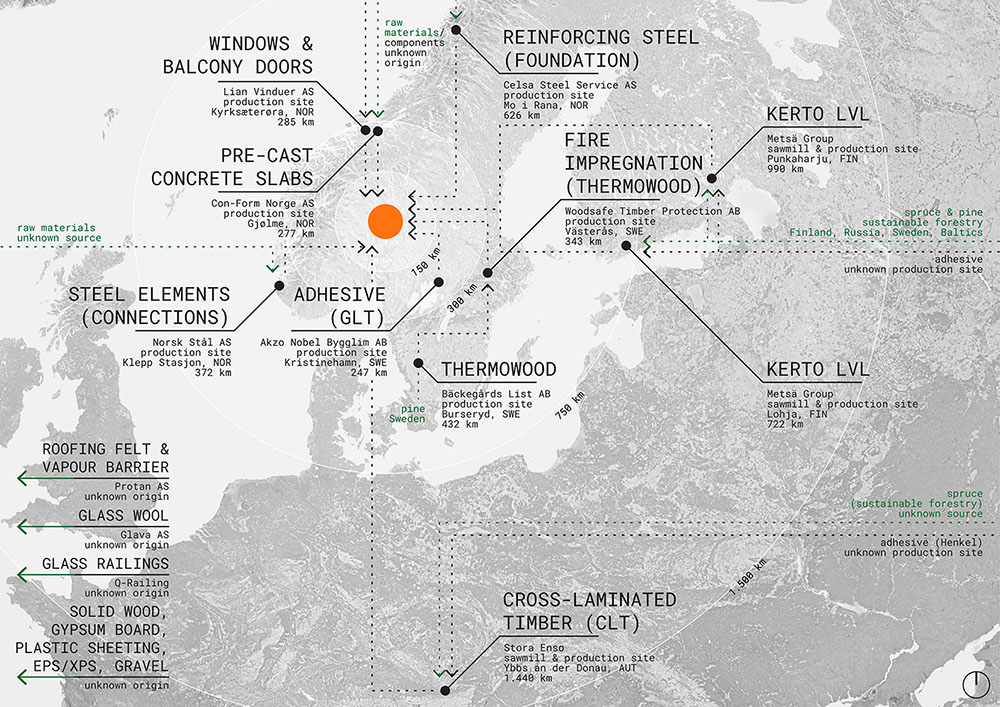