CRCLR
Berlin, Germany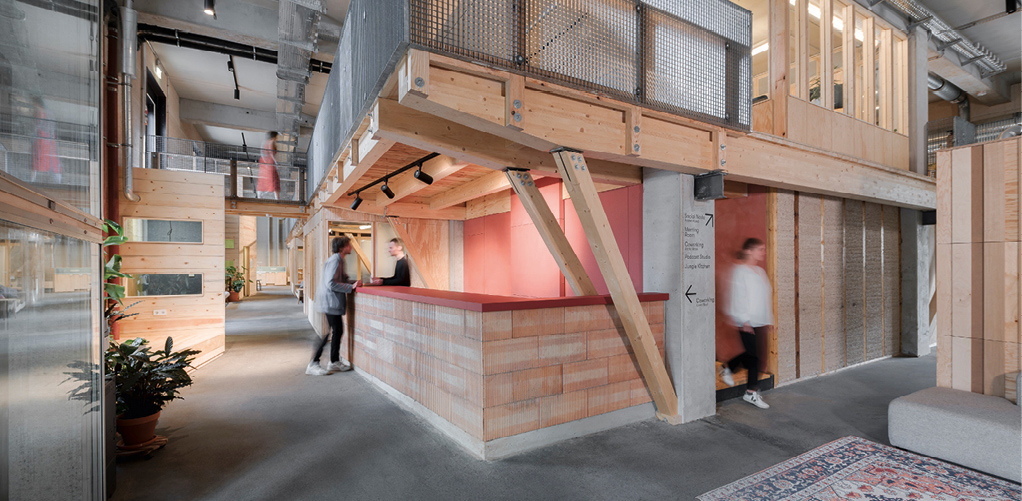
- Time
- 2019 - 2024
- Building type
- Transformation & Extension
- Client
- TRNSFRM eG
- User
- Impact HUB Berlin
- Architect
- TRNSFRM eG
- Project partners
- Die Zusammenarbeiter GmbH, LXSY, ZRS Ingenieure
- Size
- 4871 m2
- Use
- Mixed use (offices, workshops, housing)
- Website
- Link ↗
- Banner image
- TRNSFRM eG
General description
“CRCLR Haus” is a project in Berlin (Germany) that reuses a former industrial building, which was transformed into a co-working space for circular entrepreneurs and extended with housing on its rooftop. The extensions are designed for residential purposes while the big spaces below were repurposed for co-working, workshops, studios, and events. The Impact Hub Berlin took residency here in March 2022, offering 100+ workplaces, team offices, and event spaces.
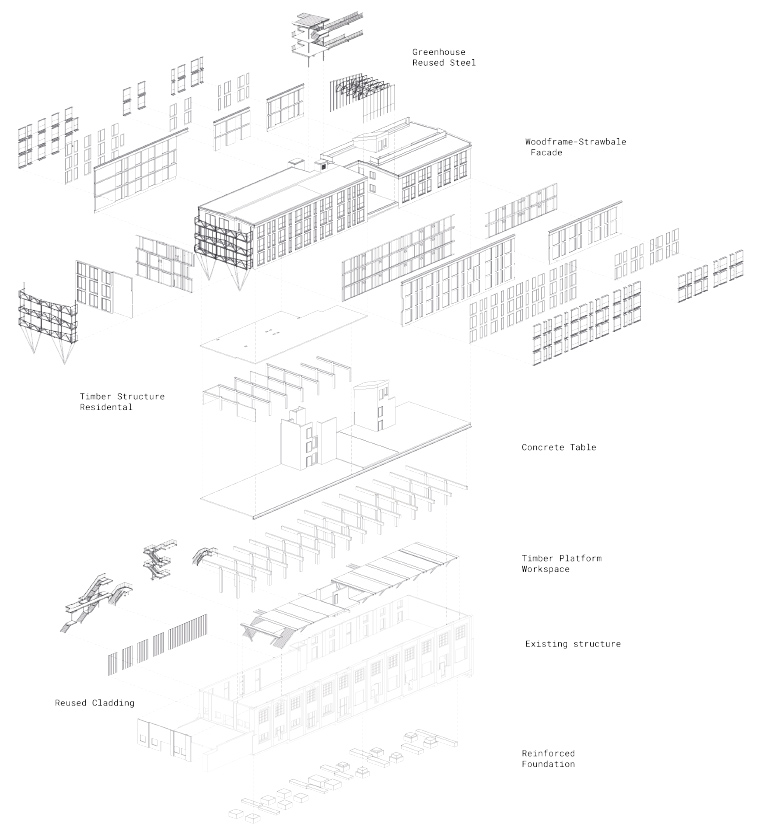
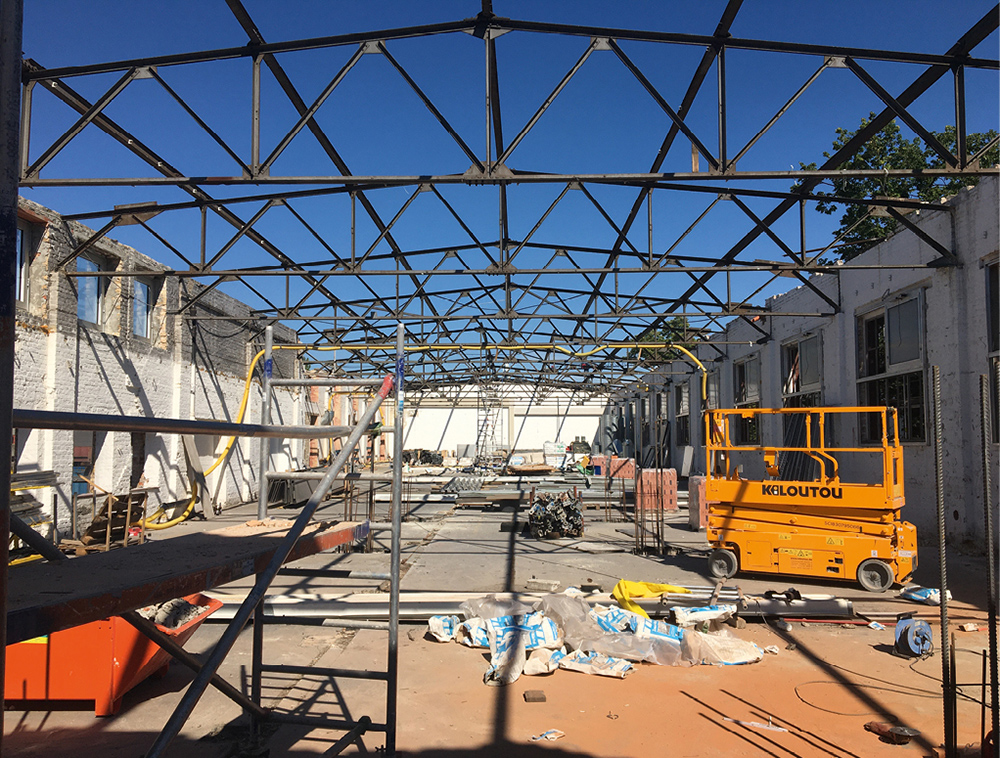
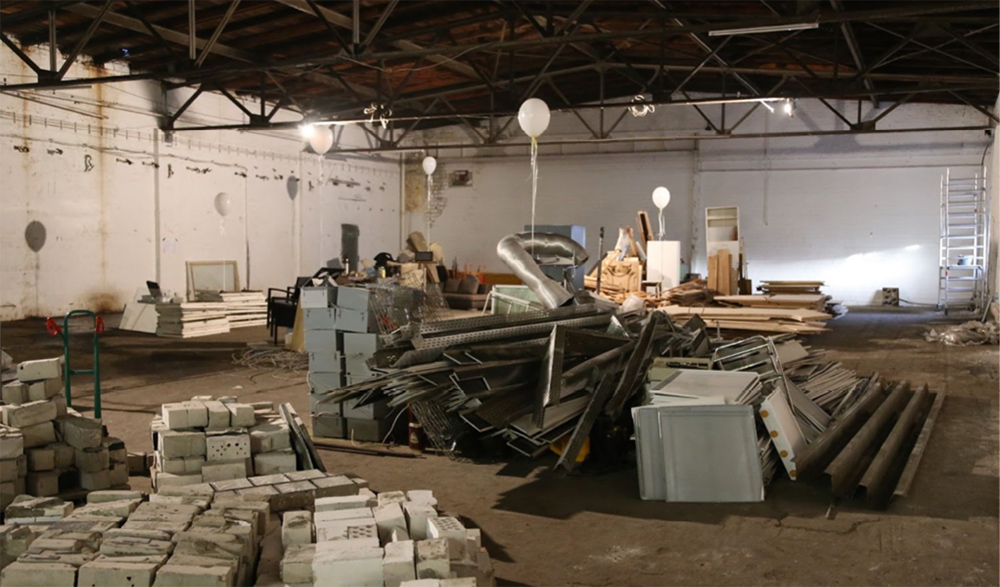
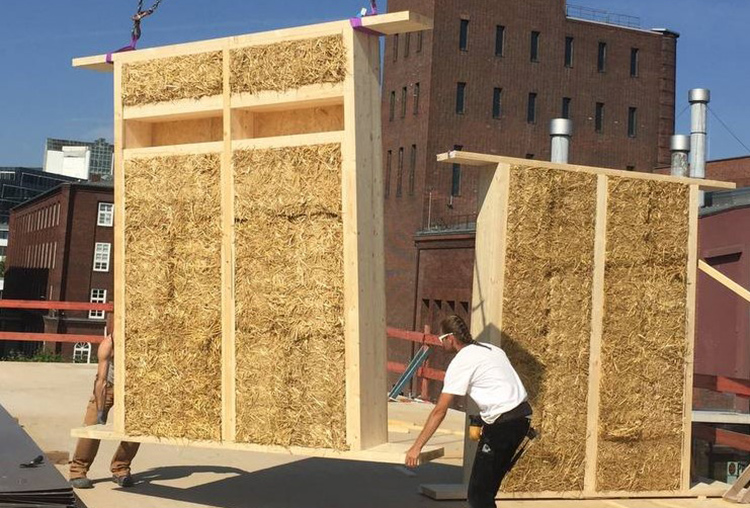
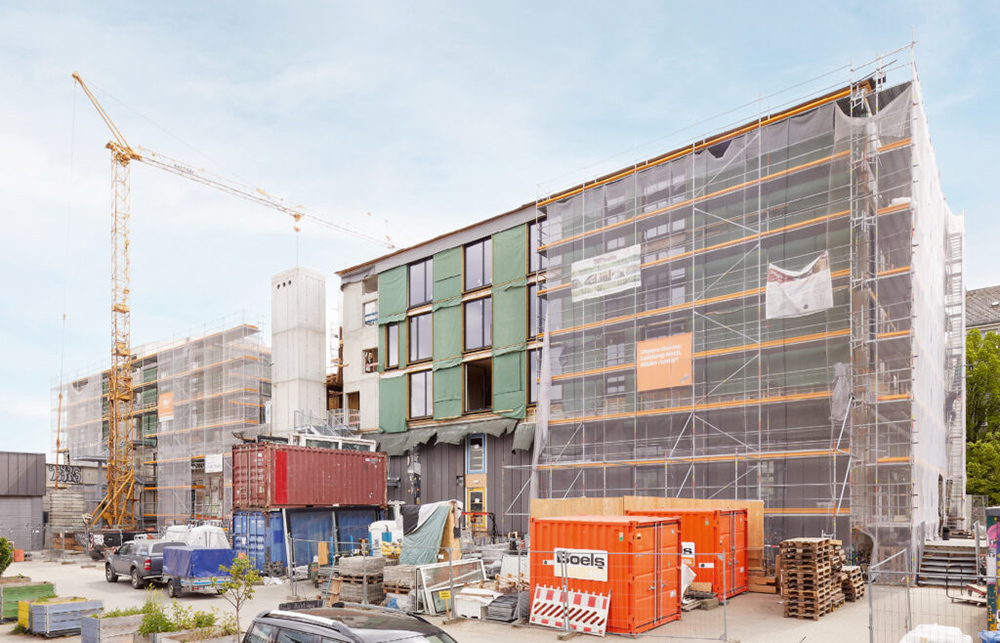
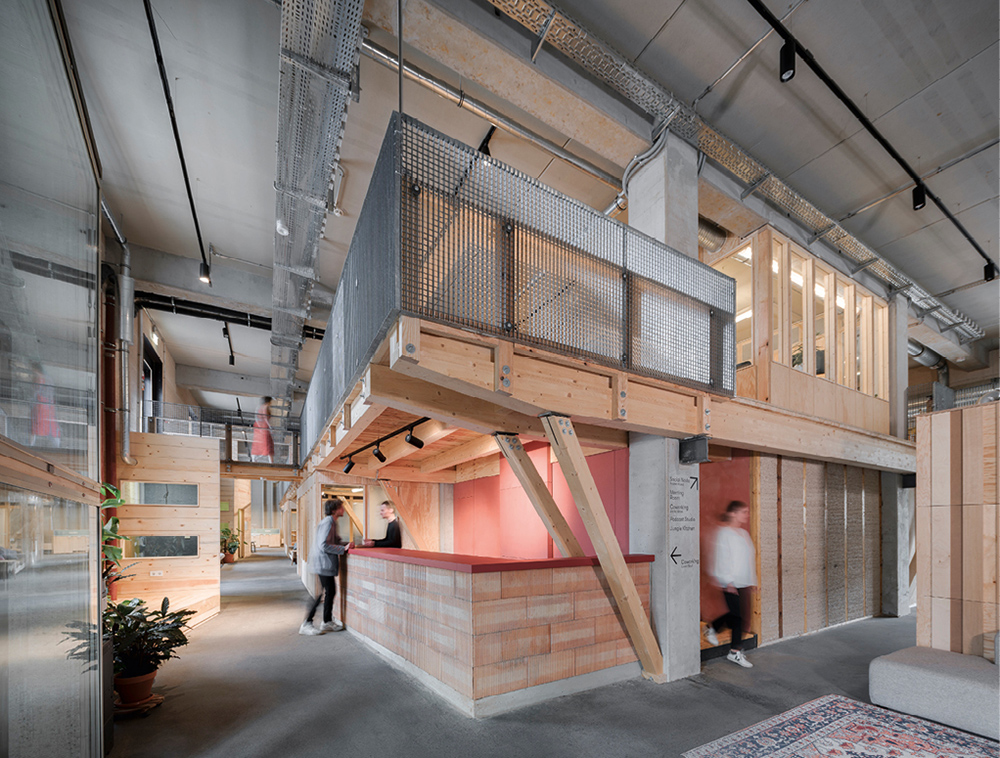
Introduction to Circularity
In the case of the CRCLR Haus, the idea of a circular building goes beyond the construction and manifests especially in its use phase. The existing building was not torn down but reinforced where necessary and the old roof-structure, insulation, and sanitary elements were reused. New elements were planned in layers and joined with reversible connectors. Technical elements with shorter life expectancies are easy to access and can be exchanged without additional destruction of cladding or flooring. Residential and commercial functions are interconnected to benefit from each other and to close energy and material loops. The interior renovation was largely done by the users themselves with approximately 70% of reused, recycled, or upcycled materials.
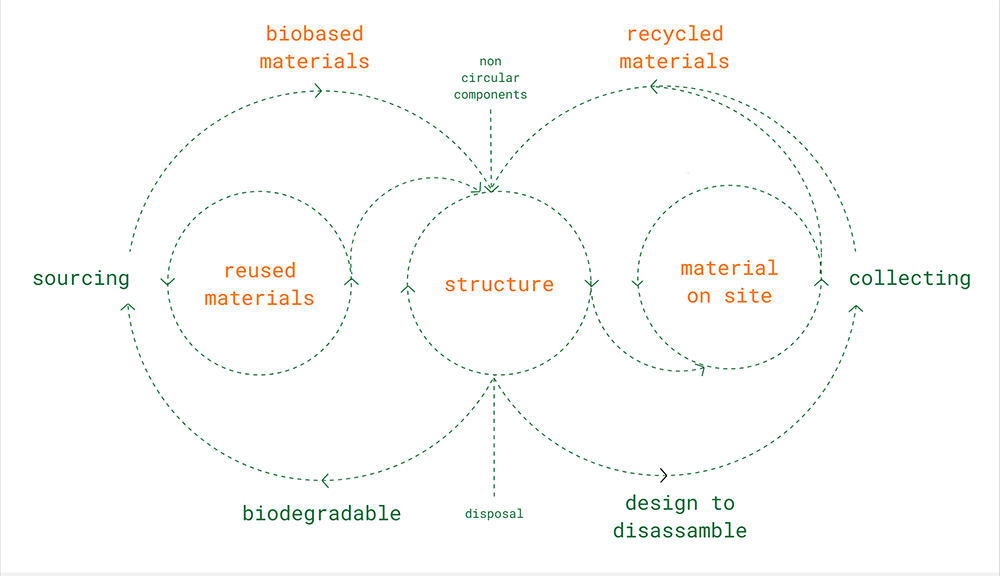
Practices
We want to persuade society to move towards a sustainable world by demonstrating the changes needed to create the circular economy, both in theory and in practice. In other words, thinking big by starting small. For everyone who doesn’t just want to talk about the circular economy but wants to start building it now, in whatever capacity (…)
Circl Website
We hope that everyone will use the new knowledge and experience we have gained through the circular construction of this building. That’s why we don’t refer to what we’ve done at Circl as ‘copyright’ but rather as right to copy
Circl Website
The goal of the initiative was to consciously use sustainable and compostable building materials to enable the resources to be returned to the natural cycle. For instance, the interior insulation of the south facade consists of recyclable or compostable materials such as wood panels, clay plaster, and wood fibre insulation boards. Hemp and clay were used for interior insulation in the window area to seal gaps in the old masonry.
The extension was planned as a timber frame construction to create adaptable spaces. One particular challenge was the fire protection for wooden structures. Despite fire protection requirements R90 and REI90, encapsulation of the load-bearing wooden components was avoided, and the charring behavior was demonstrated. Wood connectors were used to save on construction height and connection materials.
Using a straw bale construction for a passive house suitable external wall was another learning experience. Challenges arose as no company was found willing or able to undertake a project of this scale. Instead, suitable craftsmen were found and trained by experienced members of the FASBA (Fachverband Strohballenbau Deutschland e. V.). The external walls were prefabricated in elements up to 4 meters long and coated with a lime base plaster. The use of a newly developed filler from a clay plaster manufacturer for airtight connections proved promising but is not yet certified. The straw bale construction remains freely accessible for easy leak repairs.
Most of the reused components were installed as facade elements. It was easy to reuse components that are standardised, i.e., sanitary, ceramic, or shower trays because they require less preparation for reuse. The reuse of doors and windows was more complicated because of extra requirements for fire protection or energy concepts. The team brought many additional components – such as exterior windows, plumbing fixtures, and floor slabs – to the site, refurbished them, and thus retained the existing grey energy instead of installing new components. The removed steel trusses and steel purlins from the existing roof of the hall were reused for the extension as roof supports in the greenhouse and as stair stringers in a load-bearing function. Tensile tests were conducted to determine their strength, and chemical analyses were performed to demonstrate their weldability. In the future, the warranty for the reuse of steel components must be regulated legally.
Existing building components were sourced at large demolition projects in the city. The team tried to buy large quantities of the same products to ensure availability. Most of the components and materials were found at other construction sites through informal contacts. The material search was supported through the platform of Concular / Restado. It was always a challenge to find immediately fitting material “ready for deployment” at a time that matched the planning process.
Logistics was a complicated process, and there was no standardised solution: each material delivery had to be organised separately, whilst providing very detailed instructions to the logistics company. The transportation costs had to be considered, as they can easily rise if no specific instructions are provided on how and where to store the materials. Therefore, ensuring the availability of the storage space close to the construction site is essential. This space should be able to keep the materials dry and prevent damage, as the delivery of the materials works by availability and not by the time they will be installed.
Material that had to be destroyed during the renovation process was used as recycled crushed aggregate in the reinforced concrete structure. Leftovers of old insulation material were reused inside the newly built exterior doors.
Quality inspection of the components was conducted internally by the team. It was therefore important to form a pool of experts with specific knowledge about the detailed components and requirements needed for reusability. The biggest challenges were fire protection (e.g. the doors) and structural requirements. This meant that the recertification took sometimes longer than expected. To conduct this step, coordination with the product’s manufacturers and specialised companies is essential. However, not many companies are willing to account for the liability of reuse components in a newly constructed building.
The core of the realisation was based on a planning process that was tightly linked to the construction phases. Thus, a flexible / reactive planning was needed that is based on the available reused materials. When the reused components were not found, new materials had to be used. Practically, the planning had to be done by material availability. The following objectives were agreed upon with the client to enable the process:
1. Circular building as a central objective: All components and materials were used in a way that they are reusable and exclusively sourced from circular systems (biological and technical)
2. Find solutions that stay within the unchanged budget, with approval possible for up to 100%
3. Commencement of construction alongside the existing site
4. Consistent barrier-free apartments without maisonettes
5. More usable space and fewer service and technology areas
6. Improvement of the CO2 balance in construction (grey energy) and operation while achieving a high KfW55 standard with an improved, ideally passive house-compatible envelope
7. Increased usage flexibility and adaptability throughout the entire lifecycle (minimizing partitions)
8. Better alignment with the needs and desires of the users
9. Improved ratio of usable area to volume (A/V) and enhanced usability of individual and shared outdoor areas
Construction within an existing building consists of extra challenges regarding the realisation of the reusability concept. The key objective of the project was the preservation of the existing building. Fire protection requirements made the change of many openings necessary, for example, the doors had to be a minimum of 120cm wide, leading to the problem that a lot of the existing structure could not be reused.From this perspective, the approach was to build with layers, considering that the structural elements should have the longest lifetime. If new materials had to be used in the structure, the team used concrete as an element with the longest lifespan. Facades and inner construction had a higher priority in terms of application of reusable components, and also the focus here was on the demountability of components to ensure deconstruction and future changes of space use.
The old (and new) materials used in the building were also stored in a material database. It was part of the circular concept to ensure digital access of the materials and components used in the project.
Due to COVID no companies could be found to carry out parts of the building’s realisation. Following an entrepreneurial DIY-mentality, a collective consisting of a few craftsmen and many laypersons was founded to build and install windows, doors, insulation, stairs, and the facade according to a predefined circular plan.
As costs obviously play a significant role in the decision-making process, sometimes you need to compromise on intended outcomes when trying to realise a building in separable layers. The team tried to orient themselves at the price of the old materials, so that it was at least twice as cheap as the new material. However, added costs accumulated for the logistics and preparation of the reused materials.
Construction within an existing building consists of extra challenges regarding the realisation of the reusability concept. The key objective of the project was the preservation of the existing building. Fire protection requirements made the change of many openings necessary, for example, the doors had to be a minimum of 120cm wide, leading to the problem that a lot of the existing structure could not be reused.From this perspective, the approach was to build with layers, considering that the structural elements should have the longest lifetime. If new materials had to be used in the structure, the team used concrete as an element with the longest lifespan. Facades and inner construction had a higher priority in terms of application of reusable components, and also the focus here was on the demountability of components to ensure deconstruction and future changes of space use.
Material inventory and supply chains
The Material Inventory is based on the Materials analyzed in the Life Cycle Assessment of the structure. Therefore no reused Material is shown, which is mostly to be found inside the building, like sanitary elements, reused windows or doors or steel beams.
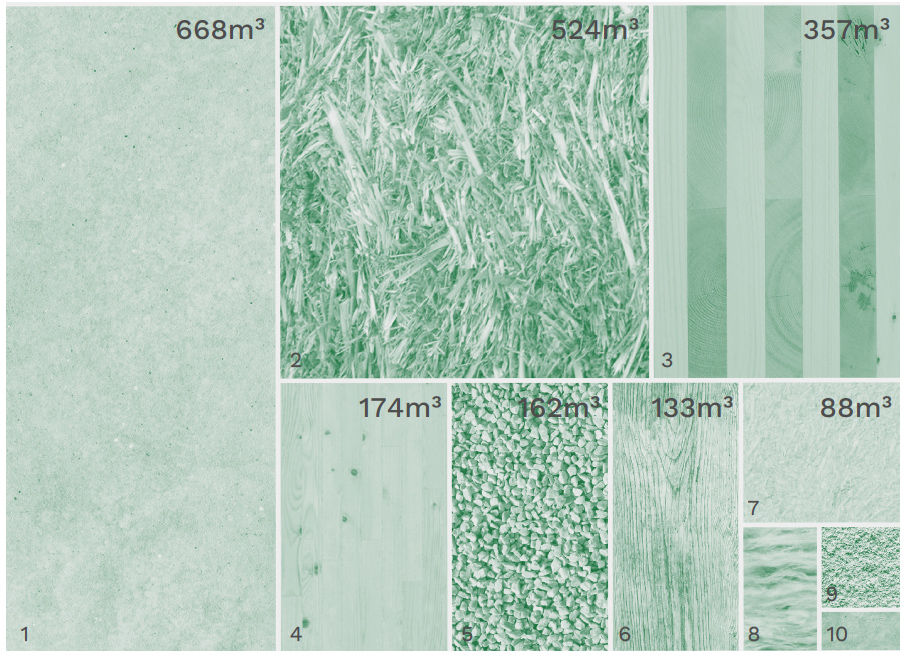
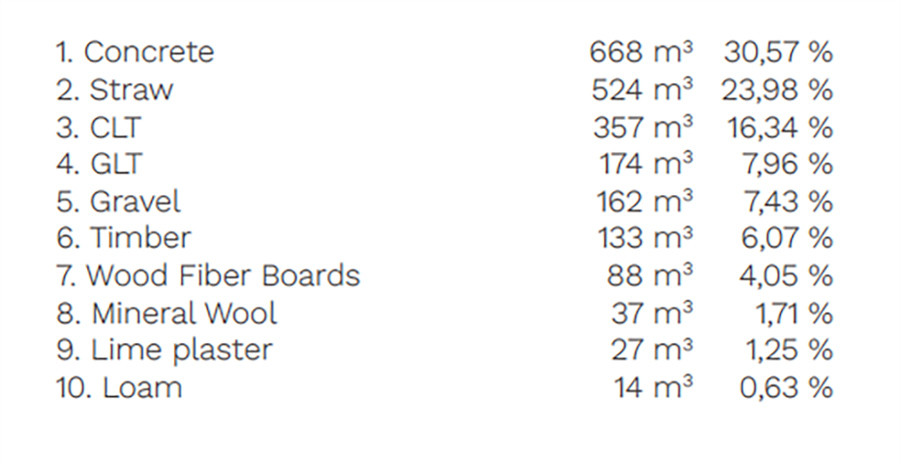