OBK 27
Paris, France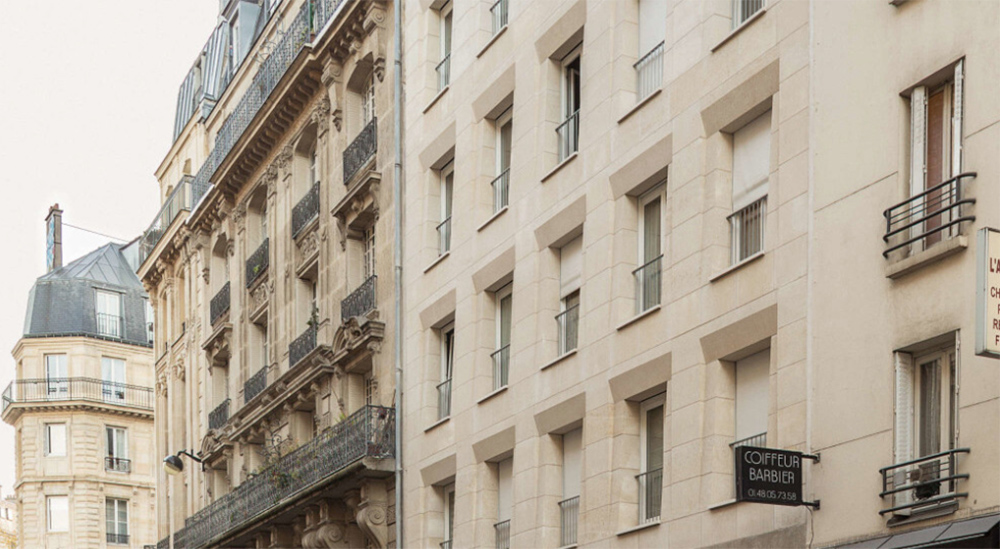
- Time
- 2017 - 2018
- Building type
- New construction
- Client
- RIVP
- Architect
- Barrault-Pressacco
- Project Partners
- LM Ingénieurs (structure and insulation), Atelux (mass flows), ALP Ingénierie (financing), QCS Services (acoustics)
- Size
- 1280 m2
- Use
- Mixed-use (housing, commercial)
- Website
- Link ↗
- Banner image
- Giaime Meloni
General description
The building of Barrault-Pressacco is situated in the 11th district of Paris and has 17 apartments constructed as social housing. Opting for solid stone as the primary material choice, the building seamlessly integrates with the city’s traditional architecture. The facade showcases the beauty of massive natural stone building blocks, which also serve as the main load-bearing components. Following a grid pattern, these blocks embrace the design principles of modernist architecture while departing from conventional masonry techniques.
The architectural design is based on a system of stacked columns and lintels, adorned with triangular vertical profiles in the windows. These subtle ornamentations draw inspiration from the local architectural design language, blending elements of the simple and minimalist Faubourg style with the grandeur of Haussmannian architecture. By avoiding internal load-bearing walls, the open floor plans provide a remarkable degree of flexibility while inviting ample sunlight to permeate the building.
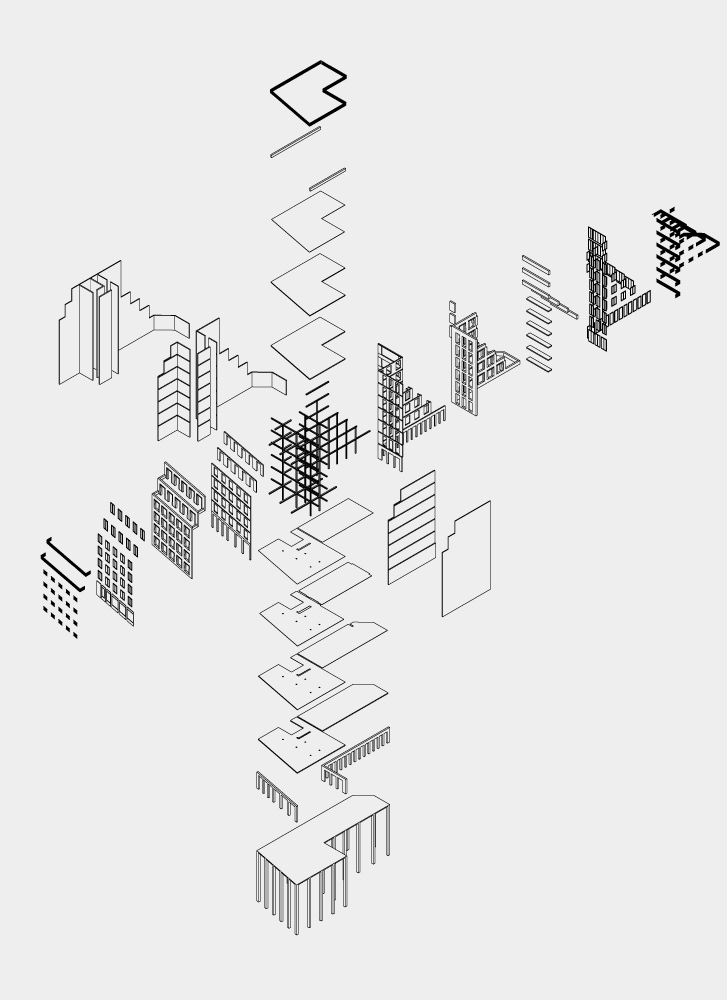
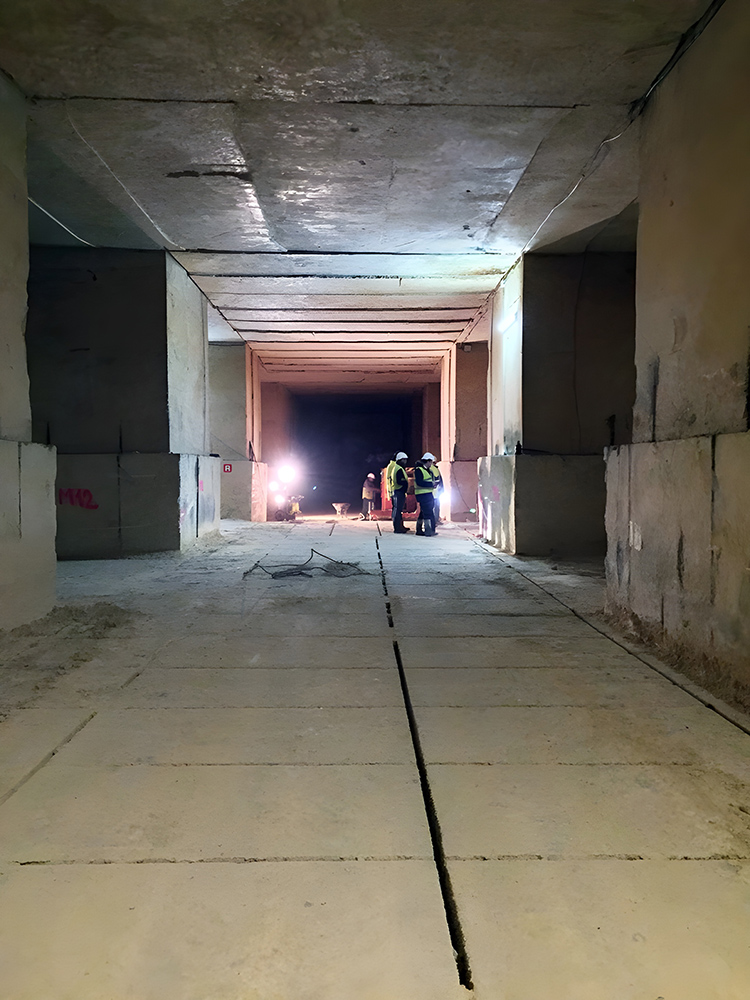
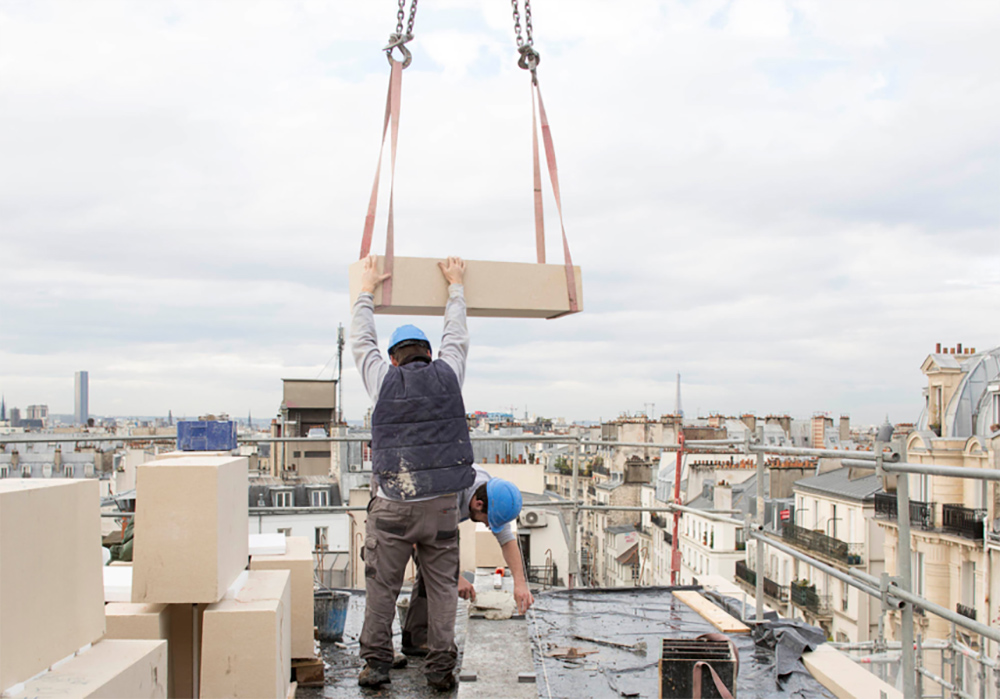
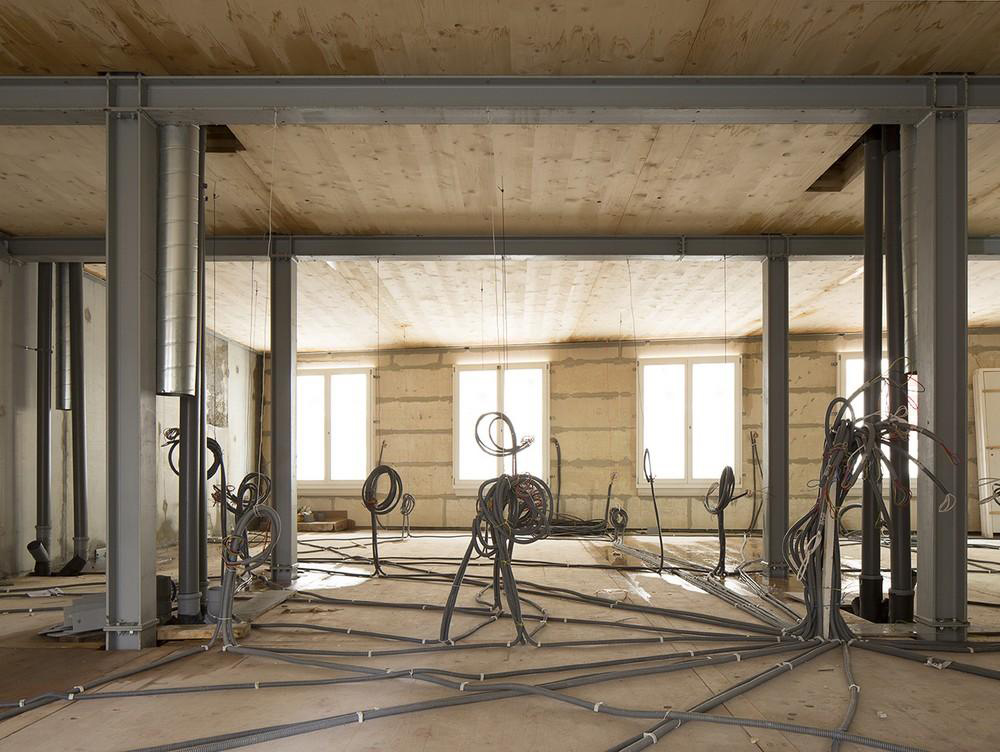
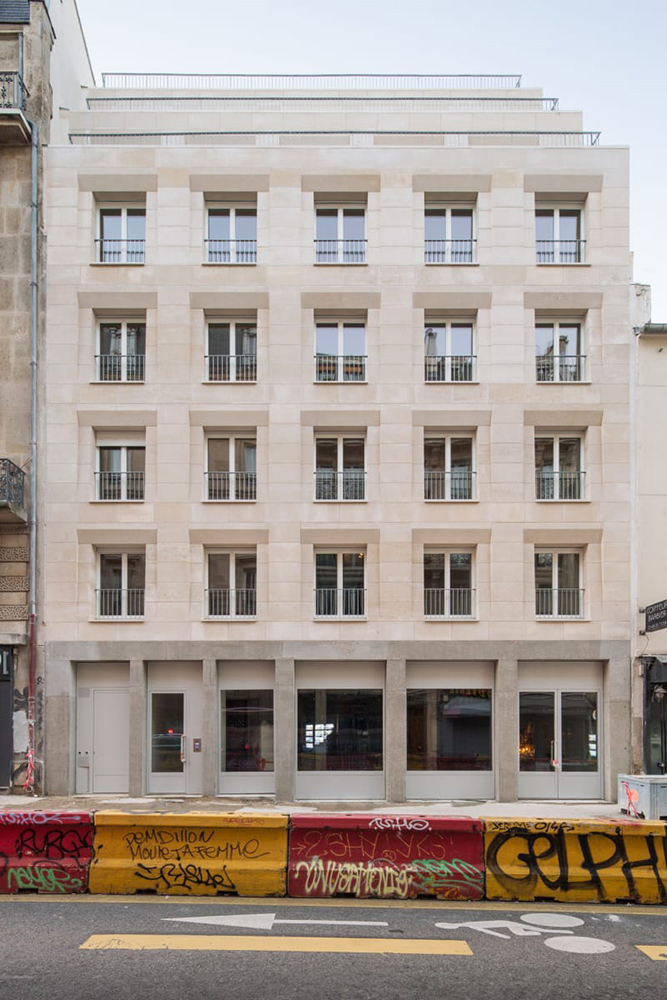
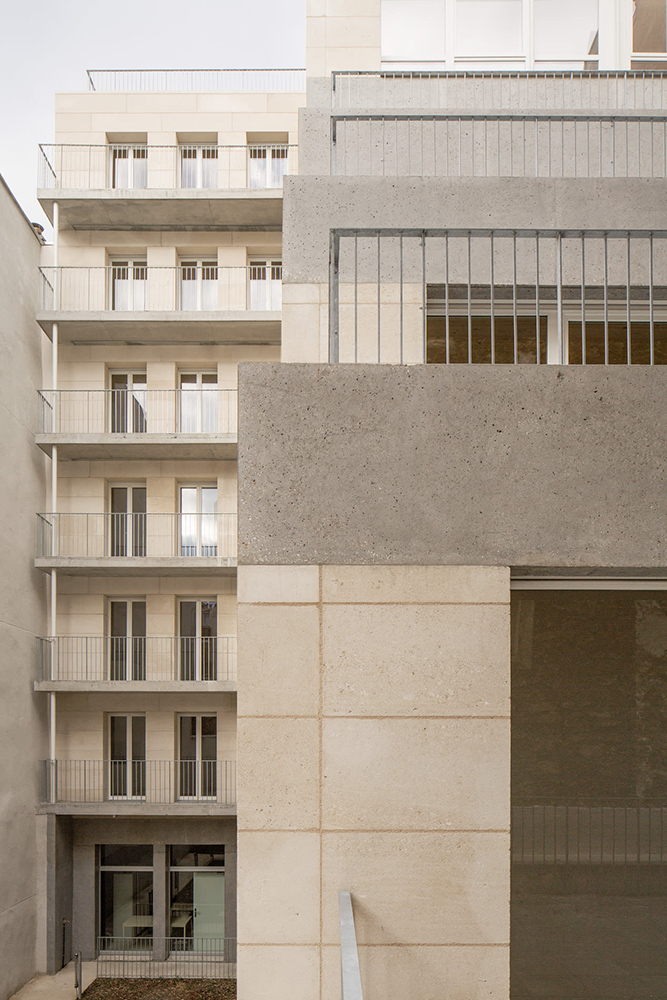
Introduction to Circularity
Constructing the building with solid stone offers numerous opportunities for circularity throughout various stages of its lifecycle. While life cycle carbon equivalent emissions were not the primary concern during the planning phase, the focus instead was on materials, assembly, architectural quality, and overall sustainability of the system. The architects aimed to create a building that would stand the test of time both technically and aesthetically.
The selection of building materials was approached holistically, taking into account their specific qualities, their role within the building system, and their long-term value. The stone blocks, which remain in their natural state without any treatment or modification aside from cutting, are regarded as an integral part of the earth. In the OBK27 building, this monolithic construction material was utilised in a sustainable, reversible, and integrated manner, allowing for nearly infinite reuse and longevity.
To ensure a high-quality and easily reversible structure, the architects opted for a simple assembly method. This choice guarantees the construction of a durable building that can be disassembled and modified with relative ease, fostering adaptability and minimising waste.
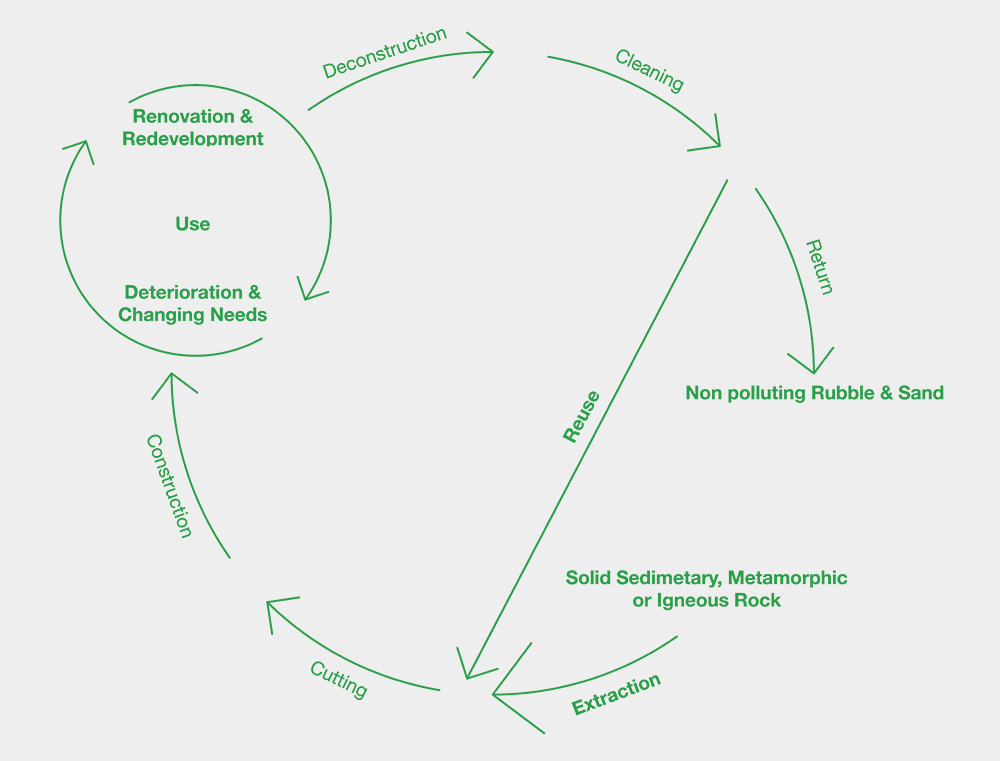
Practices
In one step you go from natural ground to architectural element.
Thibaut Barrault, architect
I hope it is a nice building but that is not enough today. It is the least to build nice today, that is not the point to me anymore. Beauty is not unimportant but it is second to collective necessity.
Thibaut Barrault, architect
Significant emphasis was placed on the construction technique as well. The architects deliberately chose a simple assembly approach to ensure the construction of a high-quality building with a strong focus on reversibility. This approach resulted in open floor plans that are free from inner load-bearing walls. This design decision allows for a remarkable level of flexibility in the use of space while enabling ample sunlight to enter unobstructed. Additionally, this construction technique facilitated the optimal placement of humid corridors and technical shafts, enhancing the functionality and efficiency of the building’s layout. Additionally, once the building’s use phase is complete, the stone material can be directly and efficiently reused, further emphasising its sustainability and circularity.
The entire building has been designed to require minimal maintenance and has a long lifespan, which is particularly beneficial considering the client’s status and the project’s social housing nature. This approach is likely to prove cost-effective over the building’s lifecycle. Given the longevity of stone, the simplicity of assembly, and the timeless aesthetics, it is crucial to consider CO2eq emissions over a long-term perspective. Although there may be higher emissions during the recycling and disposal phases, the building itself can be used for a significantly longer time compared to conventional constructions. Historical urban multi-storey buildings made of massive stone have endured for hundreds of years, making it realistic to expect that this building can last for more than 200 years with proper care. In comparison, concrete constructions typically have a lifespan of only 50-100 years.
Thanks to the comprehensive planning and the meticulous design of specific details, the structure achieves a remarkable level of reversibility, resulting in more efficient maintenance and renovation processes. For instance, the walls of the building consist of only three layers. The load-bearing natural stone structure is directly coated with hemp lime insulation, which is then covered with lime plaster. This simplified wall assembly stands in stark contrast to the numerous layers typically found in exterior walls. By reducing the number of building materials, the project also minimised the number of companies required on-site, leading to improved construction logistics. The overall design aims to create a low-maintenance building, which is especially beneficial considering the client’s philosophy.
The architects deliberately selected massive, low-carbon, and durable materials for the project. By opting for monolithic stones, massive cross-laminated timber (CLT) floors, and prefabricated steel components, the final assembly process was highly efficient, resembling the quick assembly of large Lego blocks. In modern massive stone construction, each stone takes approximately 10 minutes to be laid. Furthermore, the stone walls were carefully planned to minimise the use of different stone dimensions, enhancing logistic efficiency and reducing production costs. This approach streamlined the construction process and facilitated smoother coordination of materials on-site. By utilising prefabricated elements and optimising the logistics of stone transportation and placement, the architects achieved a faster and more efficient assembly, contributing to overall project efficiency.
The architects deliberately selected raw materials with minimal transformation and inherently low CO2eq values. As a result, the entire process from extraction and production to transportation and construction becomes carbon negative. The primary material, Brétignac sandstone, requires minimal energy for extraction and cutting. Its emissions primarily stem from the use of fossil fuels during transportation. Natural stone possesses isotropic properties, exceptional durability, and a very slow rate of ageing. It can be used in its natural state without any chemical reactions or transformations. The main minerals composing natural stone, such as quartz, feldspar, and plagioclase, remain unchanged. The massive blocks of natural stone have the remarkable ability to be reused repeatedly. Their durability, isotropic properties, monolithic and homogeneous qualities, and low rate of ageing make them highly suitable for reuse. According to Gilles Perraudin, “if you build a building out of stone, you have a new quarry because you can reuse that stone. Stone can be reused as it is, it doesn’t require recycling.” Flat bed mortar, a cement-based mortar capable of withstanding high pressure, was used for the joints between the stones. Recognising that the connection between stones is typically the weakest part of stone structures, the load-bearing mortar was protected from the elements on the exterior with a lime-based mortar, which is easier to maintain.
Material inventory and supply chains
The project’s materials are sourced from relatively distant locations in relation to the construction site. Nonetheless, the architects have made efforts to prioritise resource considerations and their respective locations, as local infrastructure for stone extraction is absent. The Brétignac stone, for instance, is extracted near Bordeaux in the southwest of France, approximately 635 km from Paris. To minimise the impact of fossil fuel-based transportation, the stones were processed in Angers, along the route from the extraction site to the construction site. Wood, although widely available, had to be imported from Austria, located approximately 1150 km from Paris. Hemp, used for insulation, is located around 200 km from the site, while lime was sourced from a distance of 300 km. France serves as the primary producer of hemp lime, facilitating localised supply chains. Steel, although available and produced locally, the priority was on good quality ore in its logistics network to reduce net emissions and waste, with transport distance being a secondary consideration. Concrete, being the most commonly used material globally, is readily available and produced locally, ensuring affordability.
The hybrid construction technique incorporates cross-laminated timber for the floors, hemp lime for insulation, steel profiles for the internal skeleton, and reinforced concrete plinths for the foundation and extension forming the ground floor.
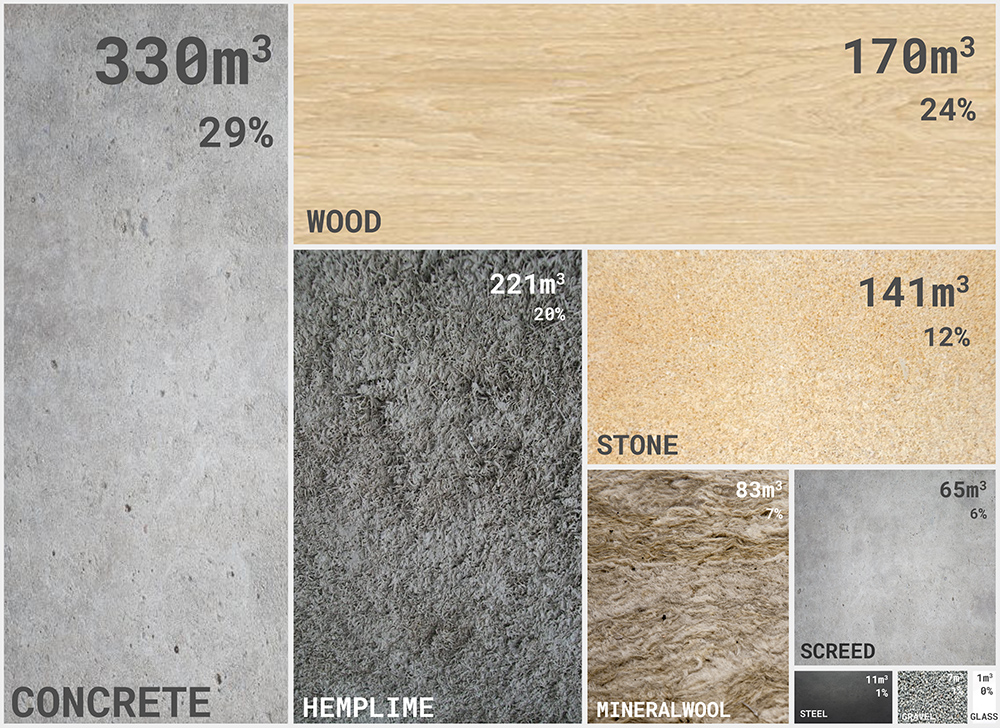
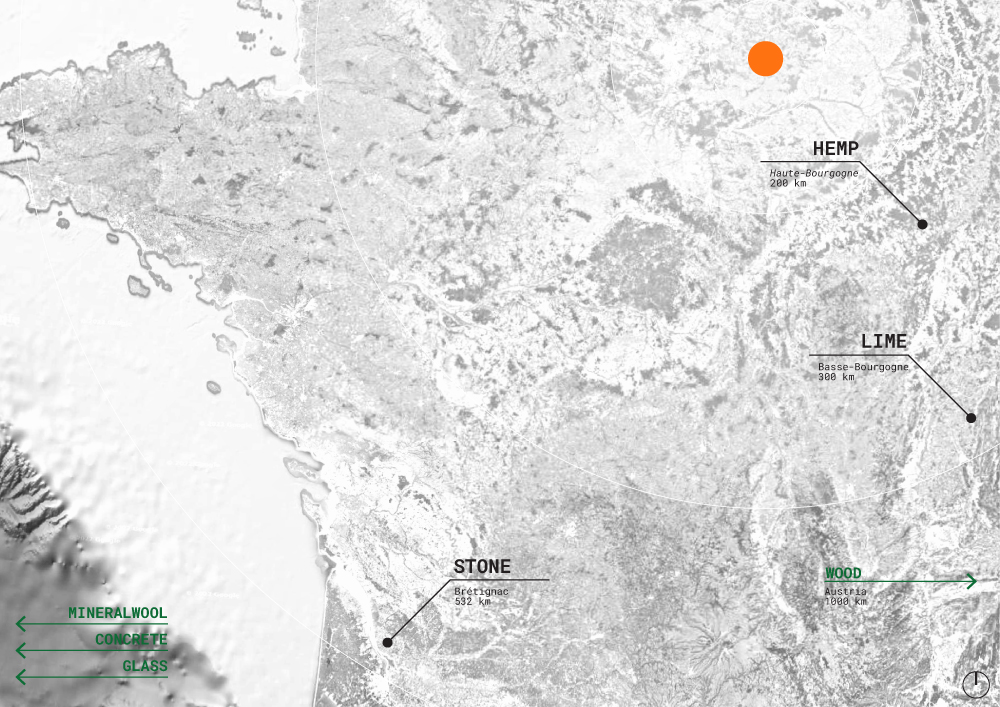