Resource Rows
Copenhagen, Denmark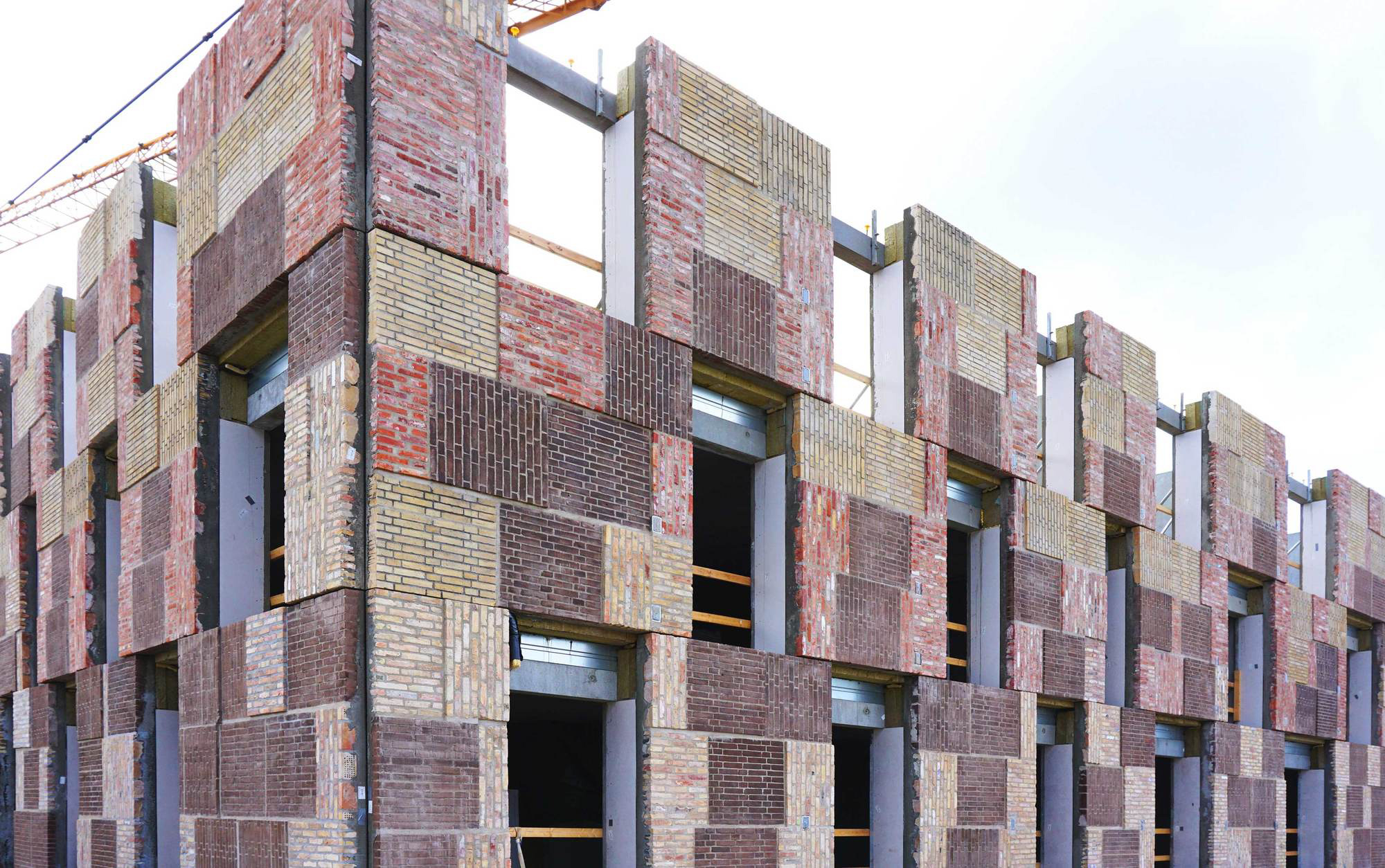
- Time
- 2015 - 2019
- Building type
- Residential
- Client
- NREP A/S
- Architect
- Anders Lendager
- Project Partners
- NREP A/S, Arkitektgruppen A/S, MOE A/S, Lendager UP
- Size
- 9148 m2
- Use
- Housing
- Website
- Link ↗
- Banner image
- Lendager
General description
Resource Rows is a residential project that created more than 9.000 m2 of housing. Around a courtyard, 29 terraced houses and 63 apartments were constructed. The building complex situated in Copenhagen (Denmark) is an example of bringing together innovation and building materials that have long passed their first life. In an intensive cooperation between the client and the team of Lendager Group, Resource Rows proves that not only reusing or recycling, but upcycling building materials is possible. Apart from the upcycling aspect of the project, water management and biodiversity are also part of the concept.
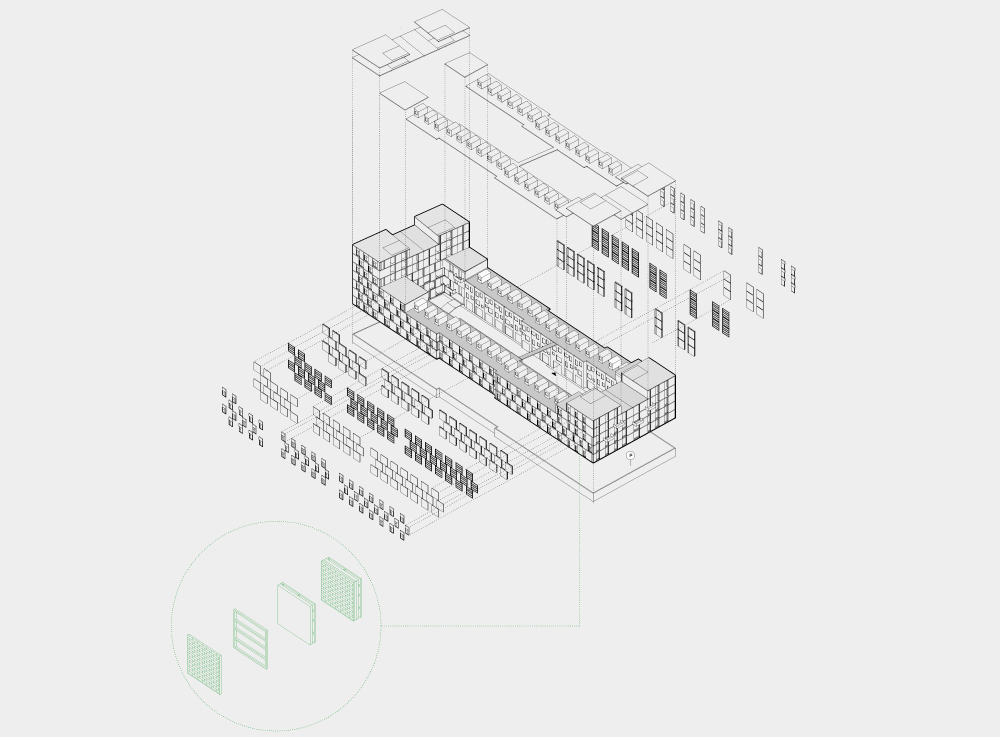
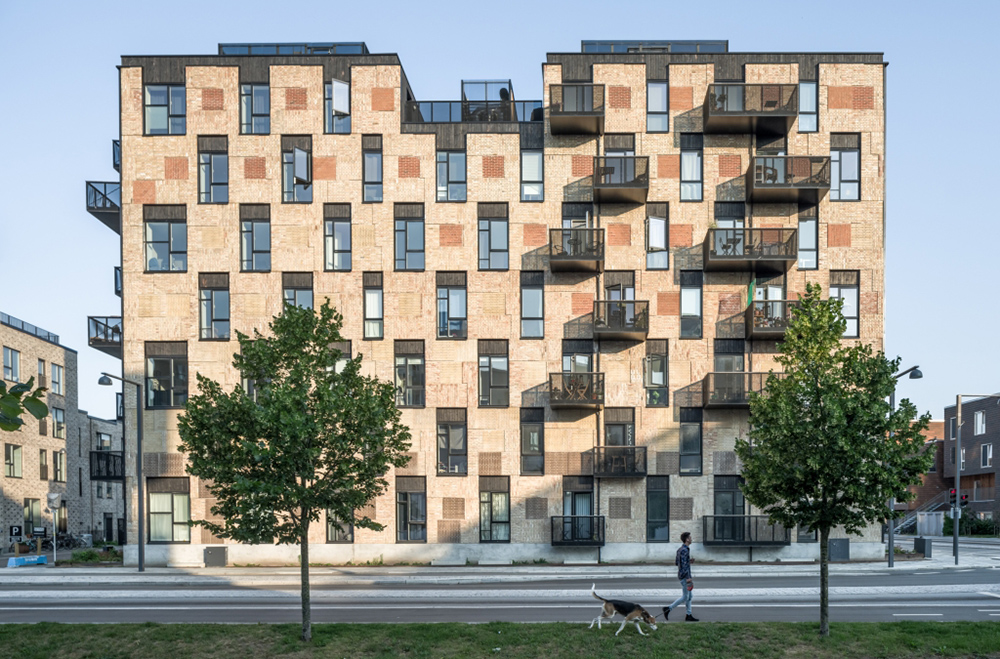
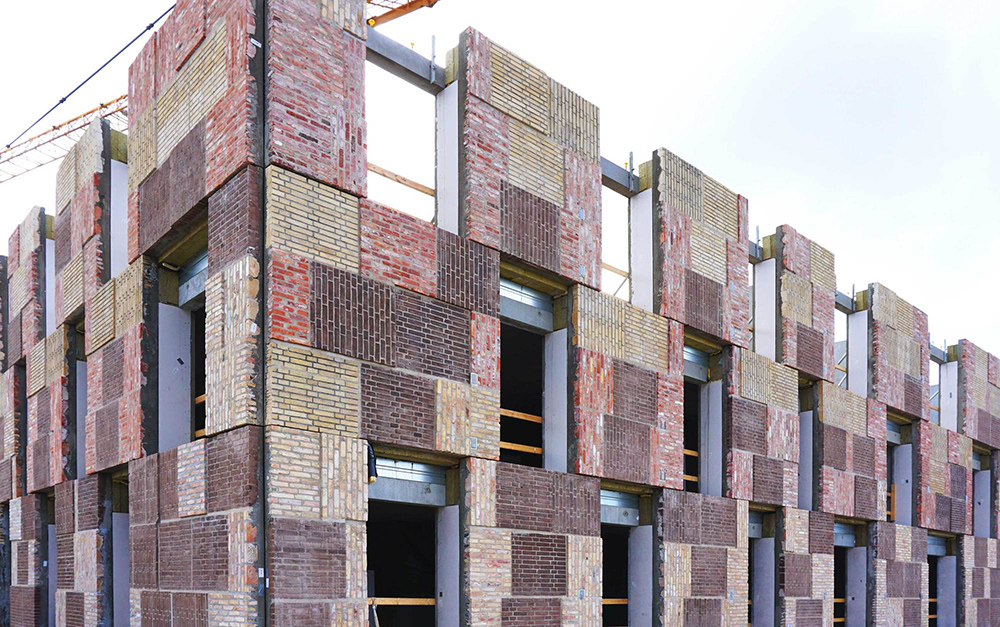
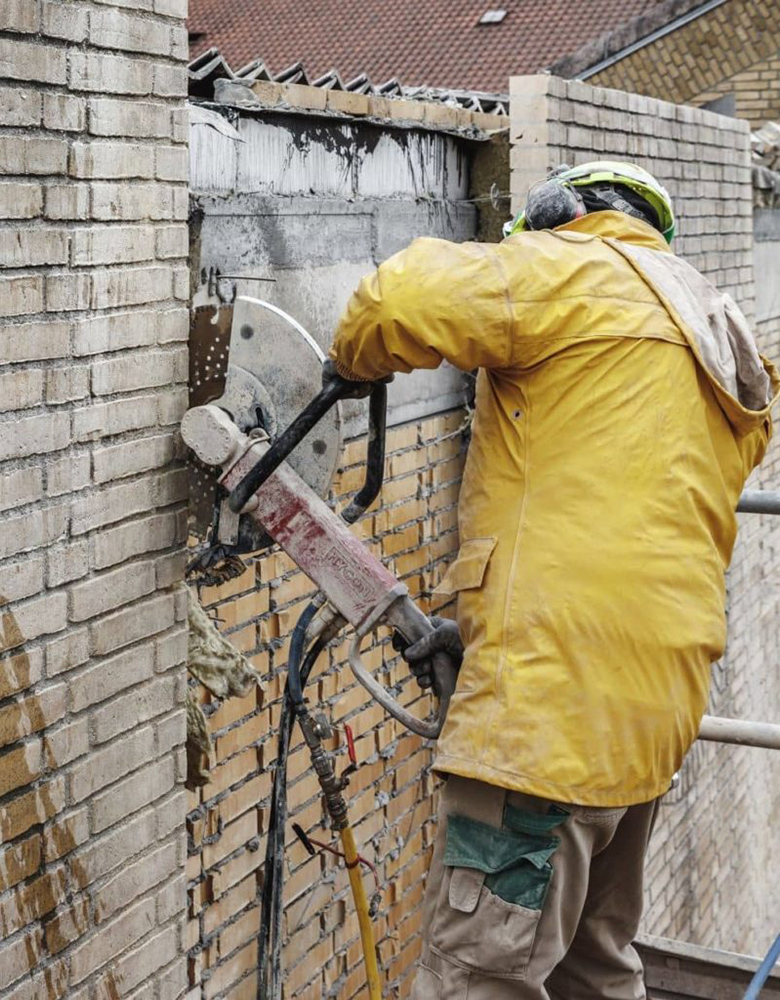
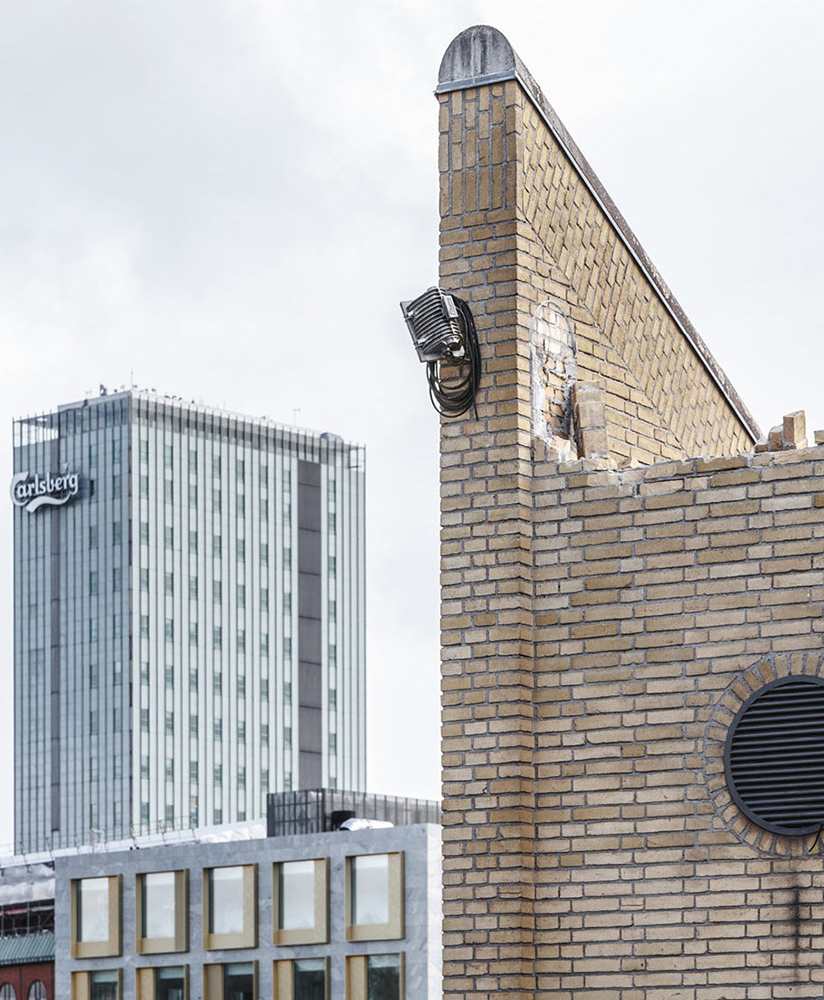
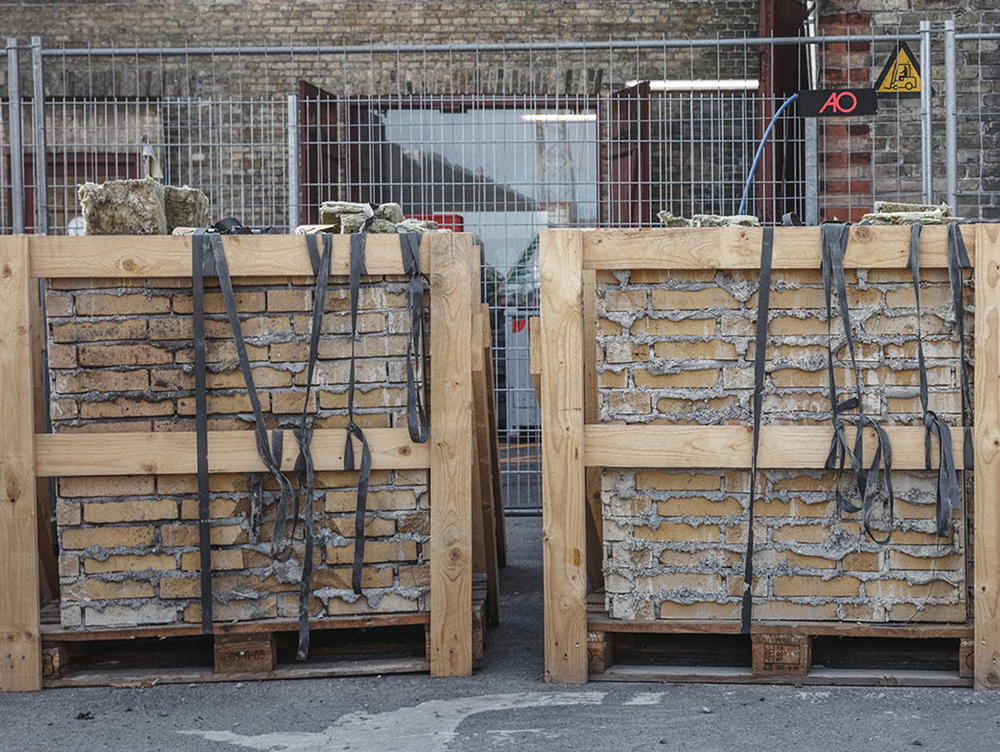
INTRODUCTION TO CIRCULARITY
In terms of circularity, the main objective was to rethink the façade by installing upcycled brick elements. The façade is composed of 39% of materials that were sourced from demolition sites, no further away than 160 km from Copenhagen. Apart from the facade, 5% of the wooden deck and 20% of the roof were upcycled. 914t of waste was saved. The approach was to treat waste materials in a way that the resulting products neither decrease in value nor only retain it, but actually increase their value. Demolition as a value-adding process opens up a new perspective to the problem of construction waste, which Lendager Group first explored at a large scale with the Resource Rows.
Practices
As a person, you must be curious about new solutions. The same goes for your organisation. If it does not have a natural curiosity, then it will be difficult.
Claus Mathiesen, builder, CEO of NREP
The architect points out that the barriers, which slow down the transformation towards a construction economy based on reused materials, are the lack of certification systems for such materials. Besides that, he sees a problem in the time- and investment-intensive nature of such construction projects including many stakeholders who have to share responsibility and coordination efforts. Since the materials used in reuse projects have previously been used in other buildings or come directly from the industry, their properties are well known, but this does not mean that the properties are readily documented. When a brick is taken from its origin and used in a new context, it must be treated as a completely new product. In order to incorporate waste materials into new buildings, The Lendager Group had to become a material producer to ensure a predictable flow of materials for the project.
Upcycling can add unique properties such as aesthetic and historic value to new developments. The brick panels were recovered from abandoned buildings in the region and create the unique chessboard pattern of the facade. The approach to recycle bricks from indestructible mortar constructions was developed by the architecture firm’s in-house subsidiary “Lendager up”. The Lendager group unlocked the upcycling potential of cement based mortar brick walls by developing a new system, the “UP Wall”, where a diamond-mounted saw was used to cut out elements of the mortar brick wall with a size of approximately 1×1 m. In comparison to a standard wall, 38% of CO2 was saved in the construction process. In a next step, these cutouts were integrated into sandwich panels where they were reinforced with concrete and insulation was added to meet the requirements of the building code. Timber was used as another recycled material, which was mainly installed on the terrace, in the treehouses, and on the facade. The dark finish of the timber used for the terraces and timber facade elements above the widows was created by burning the upper millimetres of the wood planks (Yakisugi-technology) and afterwards impregnating them with linseed oil. These measures saved a lot of waste, not only from the demolition site, but also in case the new material would have had to be newly produced. In total, Lendager Group claims to have saved 12% of CO2 emissions compared to a conventional building.
Material inventory and supply chains
“The Resource Rows” sourced many of the project’s components from local construction and demolition sites. Noteworthy is the usage of recycled brick panels that were recovered from the demolition of the Carlsberg breweries in Copenhagen and school buildings in Aarhus. In addition, the design implemented wood that was discarded after the completion of construction projects for the Copenhagen metro.
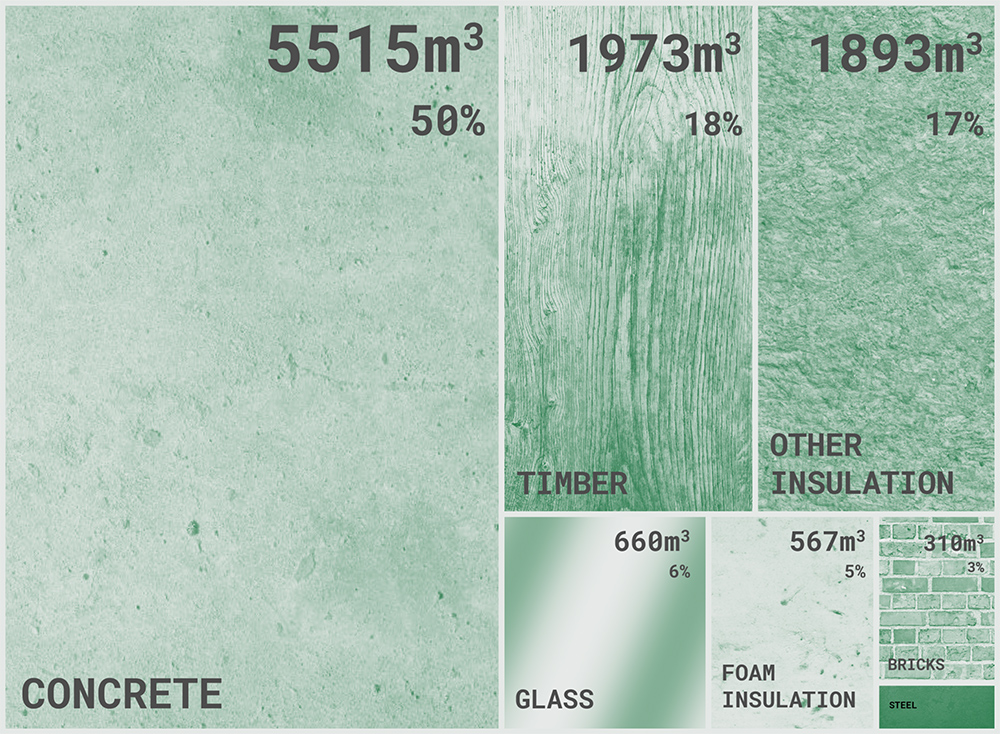
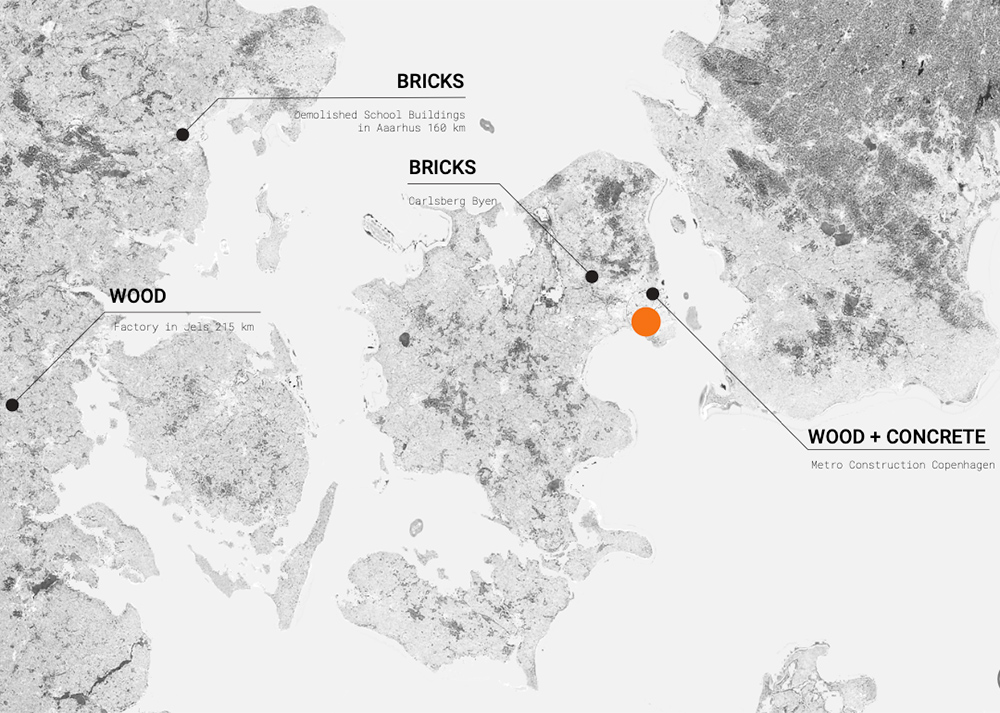